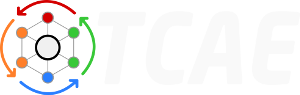
Building Wind Load CFD Simulation - Burj Al Arab
This study project shows a CFD analysis of a building wind load using simulation environment TCAE
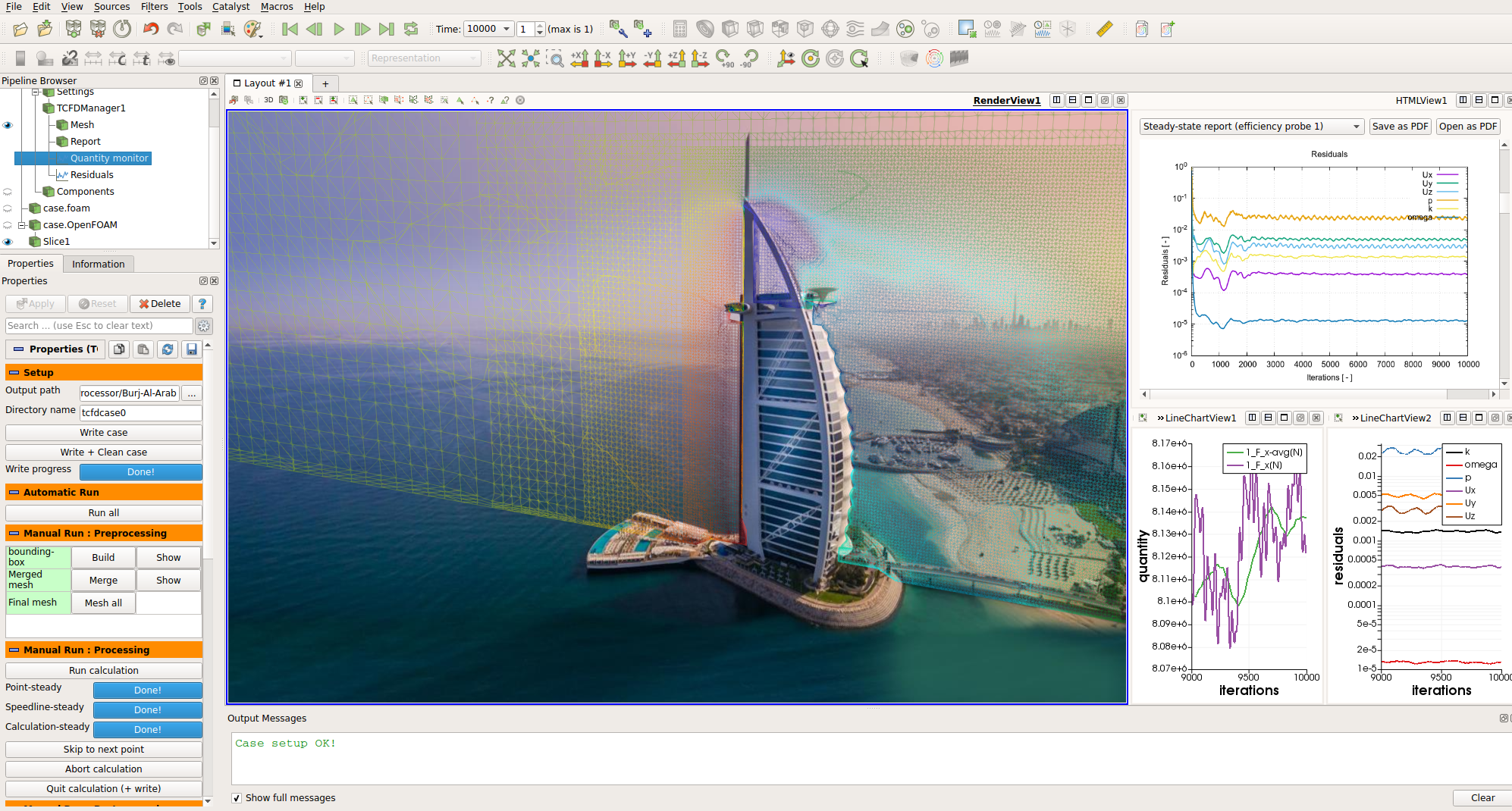
Building Wind Load CFD Simulation - Burj Al Arab
The following study is aimed at the simulations of wind-induced loads on general structures. TCFD is a general hi-tech CFD software, designed for a wide range of industrial applications. The test case used in this study is the Burj Al Arab, a luxury hotel located in Dubai, United Arab Emirates. CFD SUPPORT introduces the new generation of CFD simulations. TCFD brings an extreme increase of productivity to CFD simulations. TCFD is extremely popular project, because it successfully merged benefits of an open-source (perpetual, unlimited users, jobs, and cores, customizable, …) with benefits of commercial codes (professional support, well tested, ready for the industry, robust, accurate, automated, GUI, …).
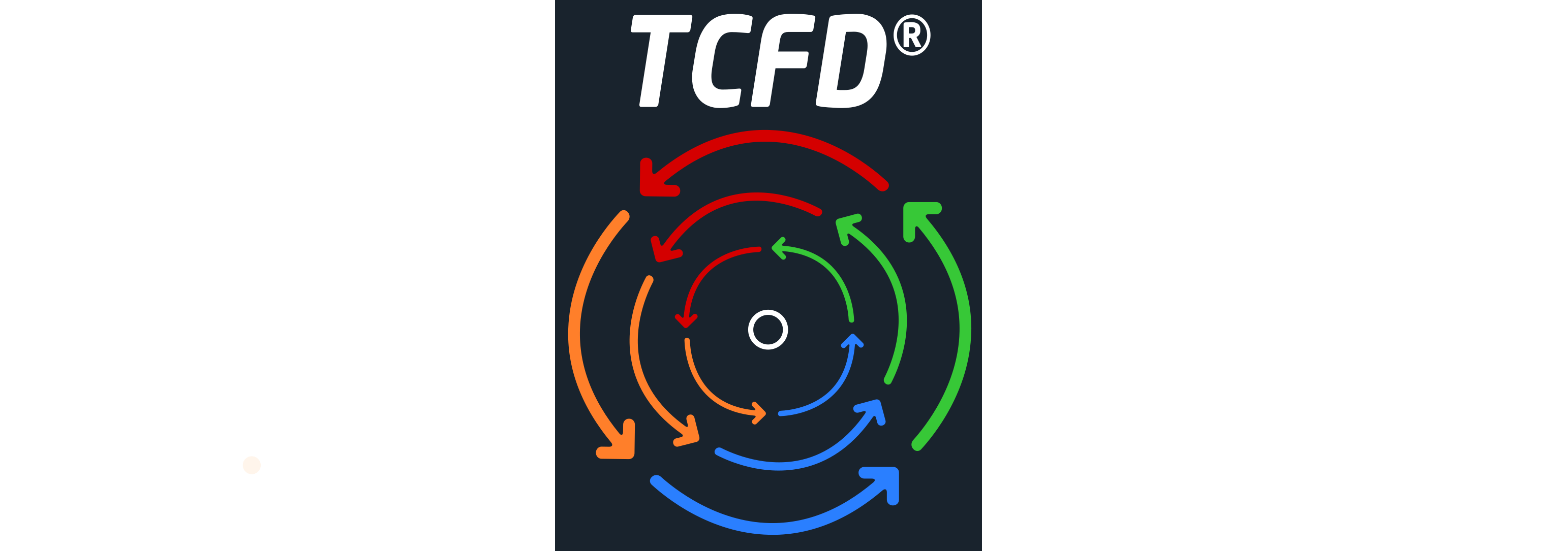
TCFD is fully automated, it can run the whole workflow by a single command: data input, new case is written down, mesh is created, case is set-up, case is simulated, results are evaluated and the results report is written down. Both GUI and batch mode. Data in – data out. TCFD is mainly focused on supporting the engineers in their real value added work. TCFD is fully automated and the beauty of TCFD is that it is the user who decides how deep to dive into a CFD or not at all. And all the options remain open at the same time.
Building Wind Load - Test Case Description
The test case used in this study is the Burj Al Arab, a luxury hotel located in Dubai, United Arab Emirates. Of the tallest hotels in the world, it is the seventh tallest (2019), although 39% of its total height is made up of non-occupiable space. Burj Al Arab stands on an artificial island 280 m (920 ft) from Jumeirah Beach and is connected to the mainland by a private curving bridge. The shape of the structure is designed to resemble the sail of a ship. It has a helipad near the roof at a height of 210 m (689 ft) above ground. Particularly for this study, it has been considered that the wind speed is 25 m/s.
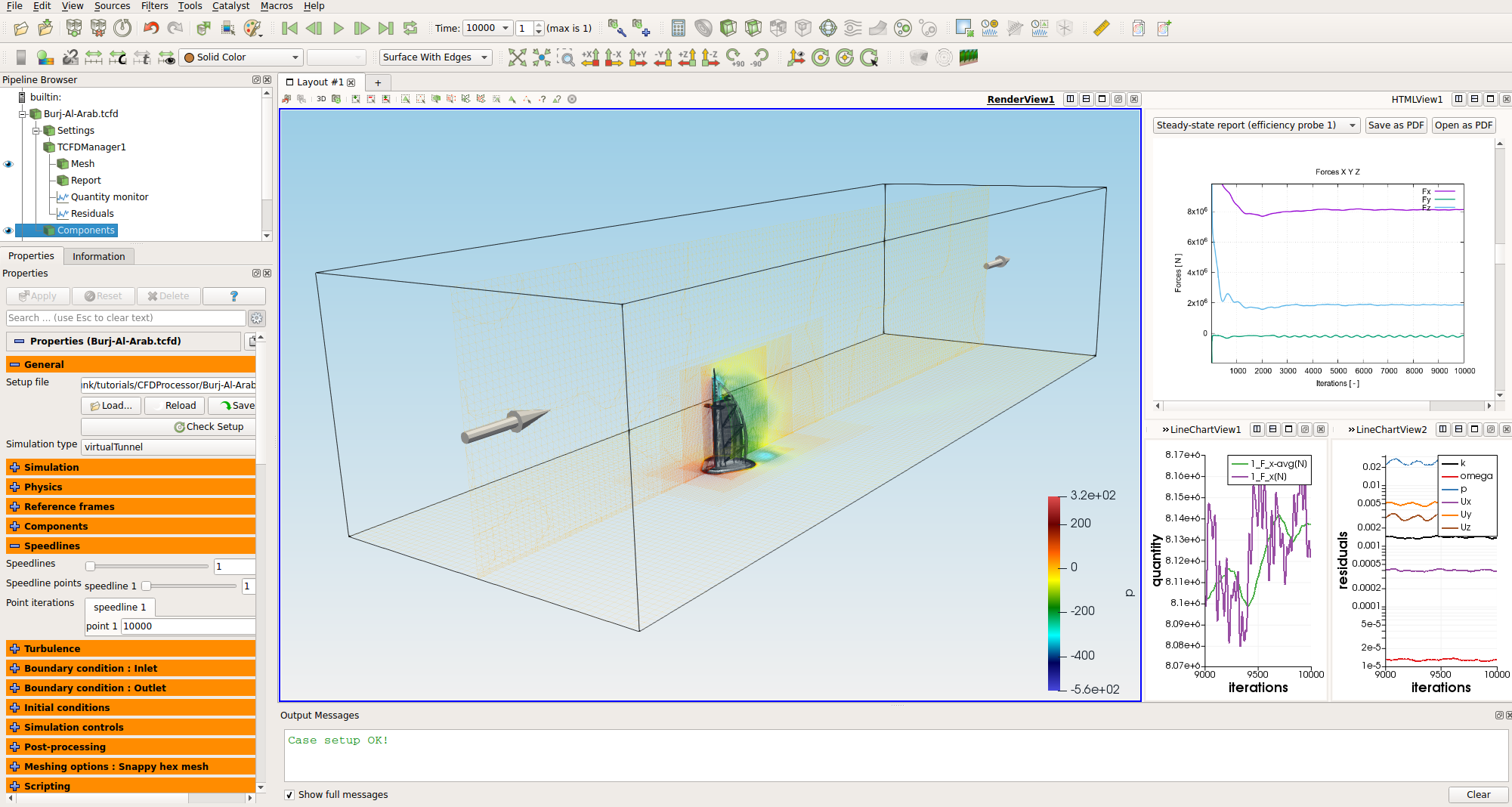
The wind attacks the building symmetrically from the seaside and the wind velocity profile is considered to be constant in time and space.The reference density is 1.2 kg/m3. Dynamic viscosity is 1.8 × 10-5 Pa⋅s. The main goal of the numerical analysis is evaluating the forces acting on the building surface.
TCFD Case Setup
TCFD, developed by company CFDSUPPORT, is a general hi-tech CFD software, designed for a wide range of industrial applications. It successfully merges the benefits of both open-source and commercial code. TCFD numerical solver is based on OpenFOAM. TCFD shows great performance at the external aerodynamics of various structures. TCFD is natively compiled for Windows and Linux operating systems. No need of any virtual systems. The engineering workflow is exactly the same on both systems. TCFD includes an automated meshing system. Based on snappyHexMesh. And also, the external meshes created in another software can be loaded. TCFD has strong postprocessing. Every simulation that is executed in TCFD, has its own HTML report with the results. Volume fields are visualized in ParaView. Integral results are saved in CSV files. In this particular case, the simulation type is Virtual Tunnel, especially designed for simulations external aerodynamics. The turbulence model is RANS k-omega SST. The finite volume mesh is created using snappyHexMesh. The virtual tunnel is 3000m long, 1000m wide, and 700m high. The mesh is well refined close to the model, including the inflation layers, to model the flow boundary layer as accurate as possible. That leads to the finite volume mesh of about 5,000,000 cells. Simulation based on such a mesh converges in eleven hours on six CPU cores.
Input data
The surface model data in .stl file format together with physical inputs are loaded in TCFD. Other option would be loading an external mesh in OpenFOAM® mesh format, or loading an MSH mesh format (Fluent mesh format). This CFD methodology employs a multi component approach, which means the model is split into a certain number of regions. In TCFD each region can have its own mesh and individual meshes comunicate via interfaces.
Grapgical interface
All the case settings are set in a graphical intergace. The TCFD graphical interface is based on ParaView. Most of the users prefer to use a graphical interface for case setup and then decide for example to use the command line for cluster run. The workflow is very flexible and the command line vs GUI decision is always on the user.
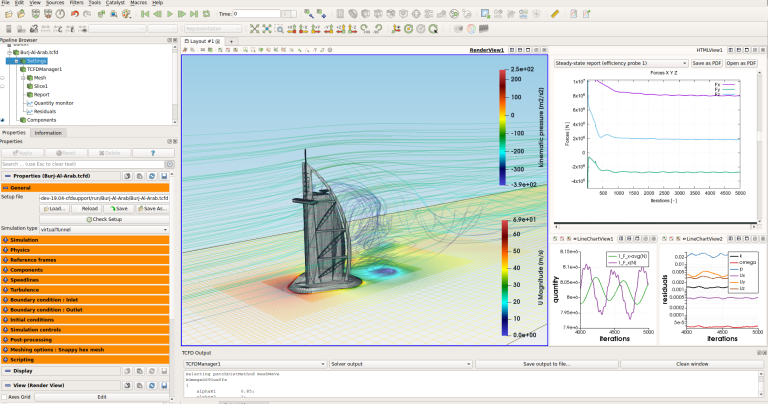
Mesh
In this particular case, the simulation model has just one component. The meshe is created automatically for within snappyHexMesh. Any number of model components is allowed.
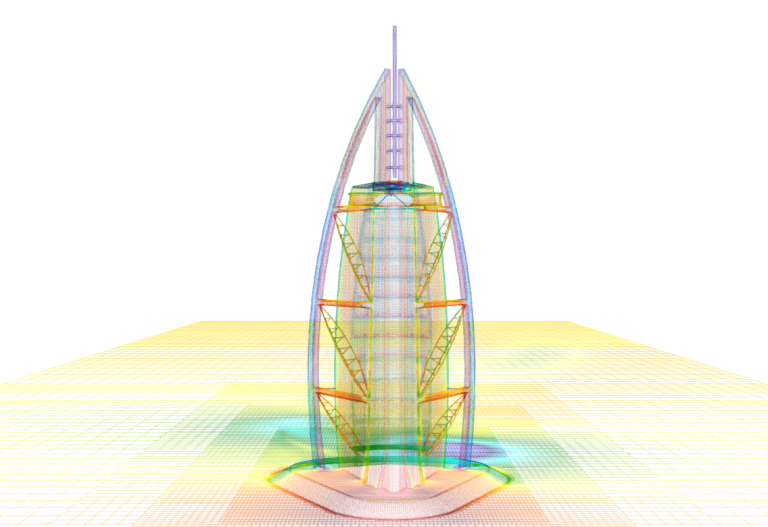
The component graph
Any project simulated in TCFD has its component graph. The component graph shows how the components are organized – the model topology. What is the inlet, the outlet and how the components are connected via interfaces.
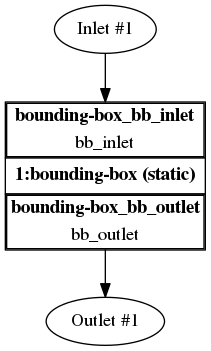
CFD Simulation Set-up
- Incompressible flow model
- Steady-state flow model
- Medium: Air
- Viscosity: ν = 1.5e-5 [m2/s]
- Turbulence Model: k-ω SST
- Mesh: snappyHexMesh
- Mesh Cells: 5,000,000
- CPU time (steady-state): 66 [core.hours]
For more details of CFD Simulation Set-up see TCFD Manual.
Running CFD Simulation
The simulation can be run on any number of parallel processors. Immediately after the simulation is started, the user can follow the progress of all the important quantities in a HTML report: forces acting on the building surface, flow rates, residuals, pressure and many others. These run-time functions give the user valuable information of the simulation convergence and also the availability to stop the simulation before its expected end.
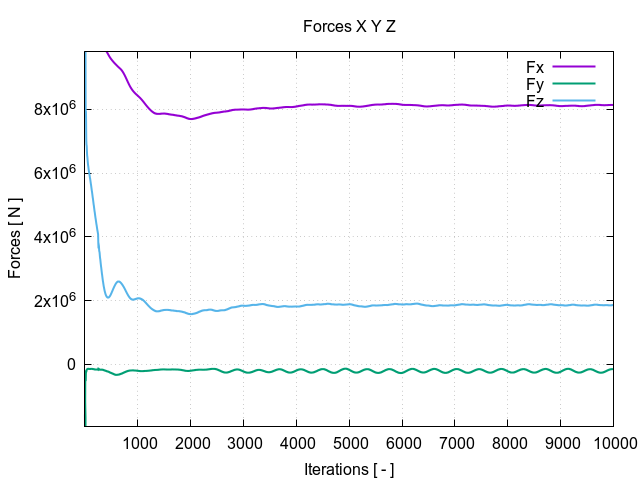
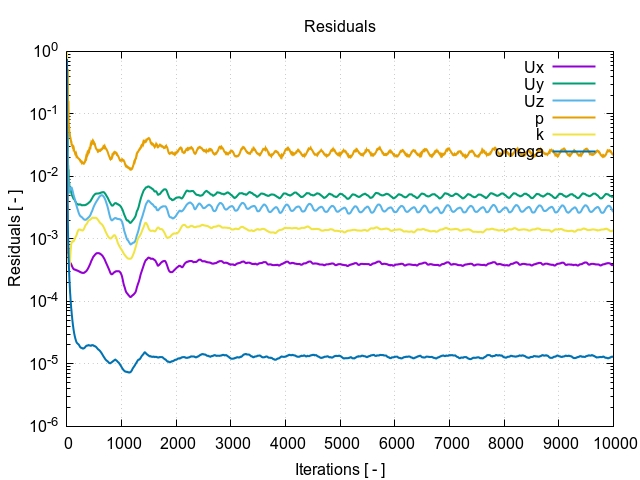
Every simulation performed in TCFD has its report in web responsive .html and pdf format: Burj Al Arab – Results Report.
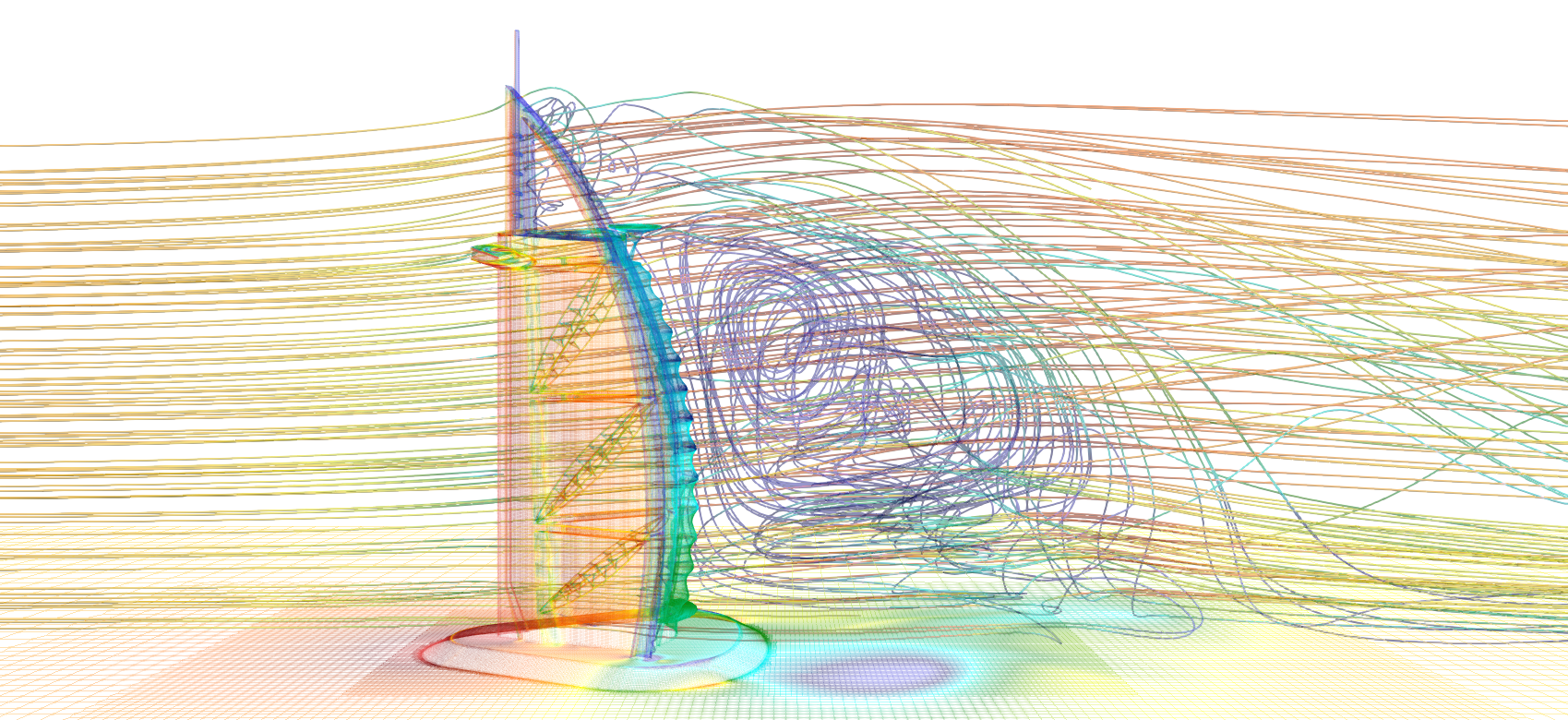
Please contact us for further information.
Download TCAE Tutorial - Building Simulation
File name: Burj-Al-Arab-TCAE-Tutorial-21.09.zip
File size: 1 MB
Tutorial Features: CFD, FEA, FSI, TCAE, TMESH, TCFD, TFEA, SIMULATION, FDA PUMP, RADIAL PUMP, CENTRIFUGAL PUMP, TURBOMACHINERY, INCOMPRESSIBLE FLOW, DEFORMATION, DISPLACEMENT, STRESS, MODAL ANALYSIS, INCOMPRESSIBLE, RANS, BLOOD FLOW, STEADY-STATE, AUTOMATION, WORKFLOW, RADIAL FLOW, FULL IMPELLER, SNAPPYHEXMESH, NETGEN, 3 COMPONENTS, RPM=3500, R=30mm