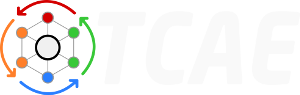
Pelton Distributor CFD Simulation
This case study shows a complex CFD analysis of Pelton distributor using simulation environment TCAE
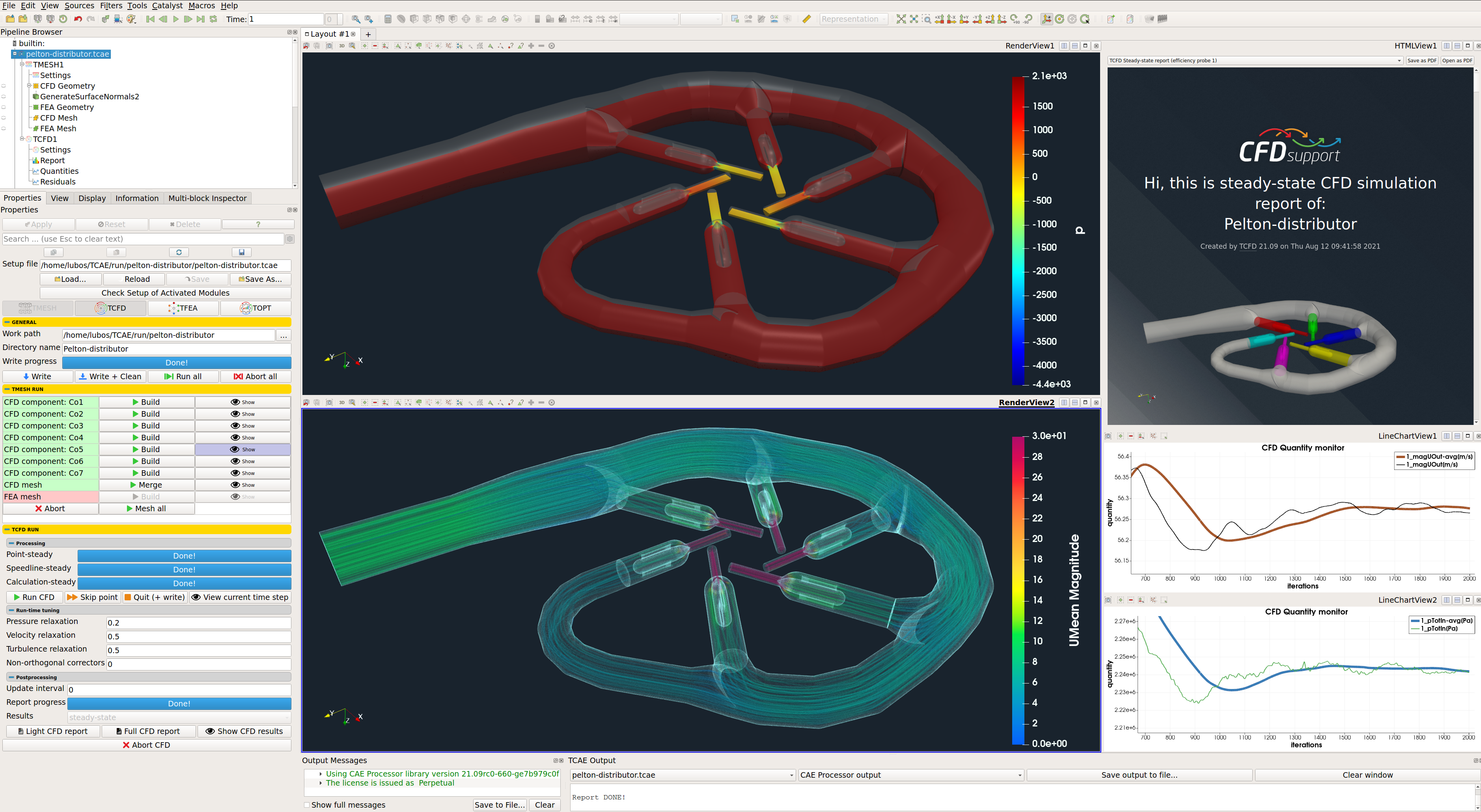
Pelton distributor simulation Introdution
This study presents a complex step-by-step analysis of a Pelton distributor from its preprocessing to an advanced CFD simulation analysis and postprocessing. The simulation software used for this analysis is TCAE – a comprehensive simulation environment based on open-source. The main goal of this study is to show in detail how to make a comprehensive CFD analysis of the Pelton distributor. Specifically, at Pelton distributors, it is important to maintain the equally distributed flow-rate at the distributor nozzles. Another important factor is avoiding pressure losses in the distributor.
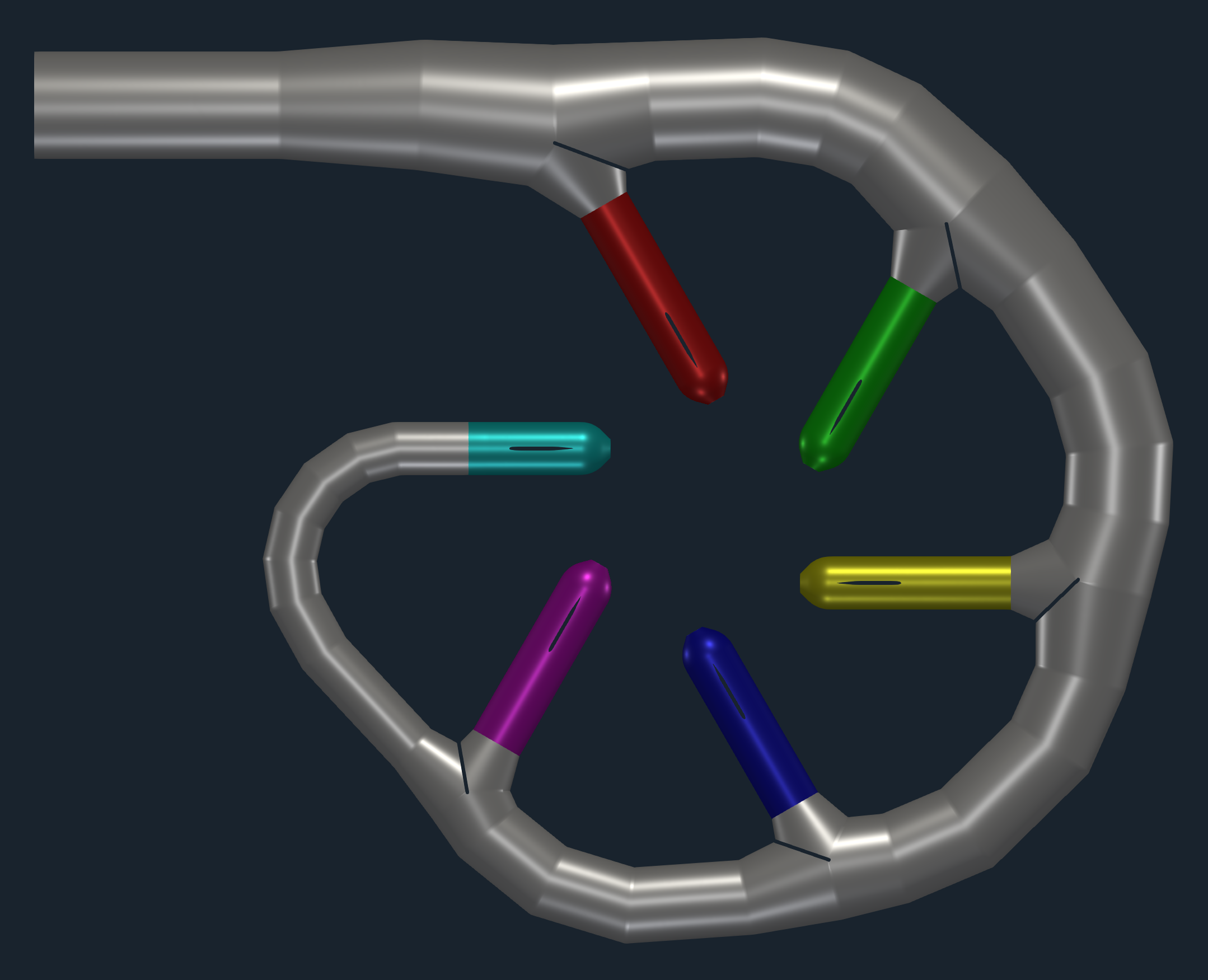
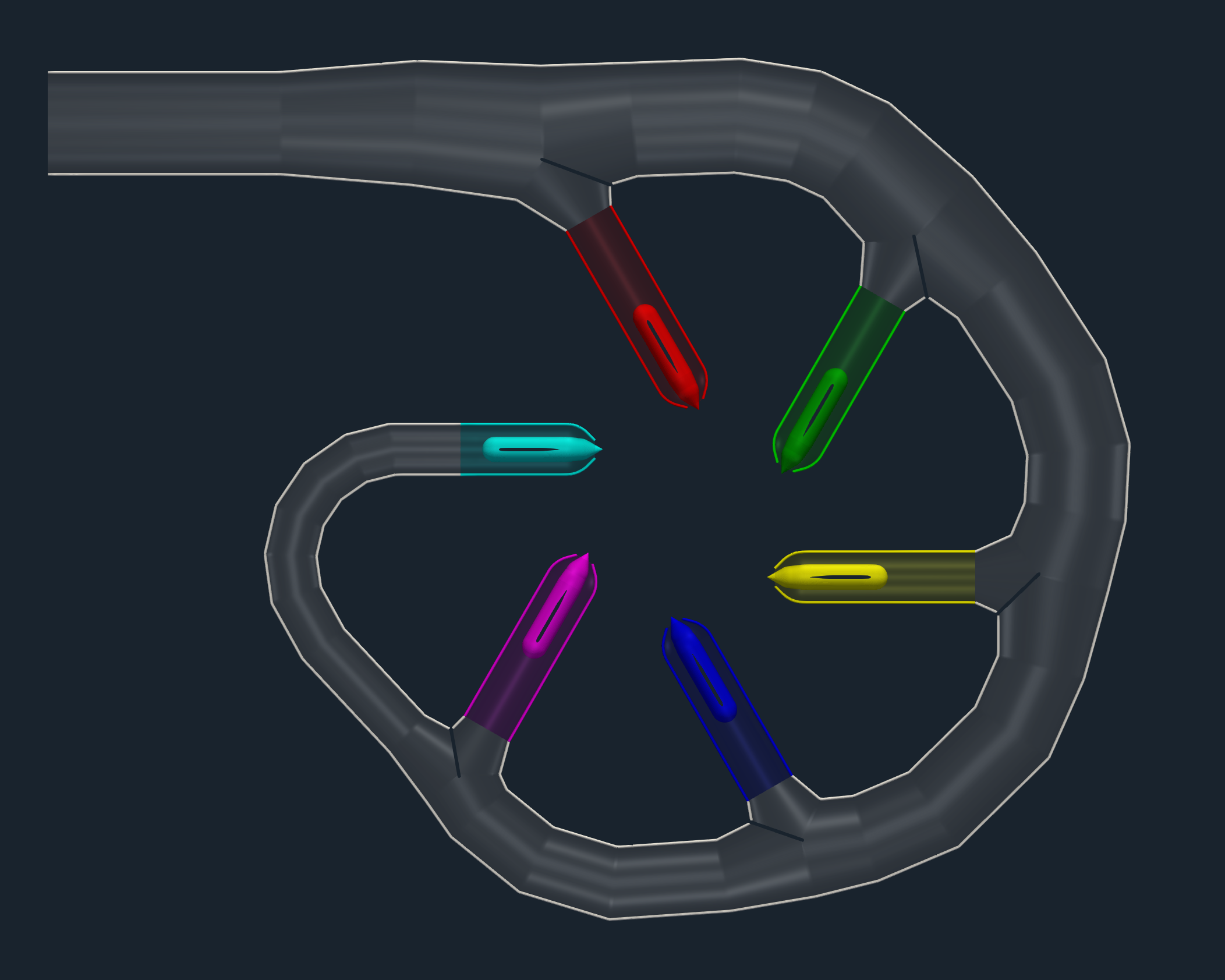
Pelton distributor design
A typical input for a detailed simulation analysis is a watertight (wet) surface model in form of STL surface. For CFD simulation, it is needed to have a closed watertight model (sometimes called waterproof, or model negative, or wet surface) of the fan inner parts where the fluid flows. If FEA analysis is involced, it is needed to have a closed surface model of solid of the impeller in form of a single one STL surface.
In general, there are multiple ways how the Pelton distributor model can be created. The CAD model of the Pelton distributor can be generally created in any CAD software manually or in an automated way via parametric model. Or, the surface model of a Pelton distributor can be created in an open-source software like for example Salome, FreeCAD, or Open Cascade. In any case, a Pelton distributor can be described with the help of a set of parameters that describe all its important shapes and measures.
Pelton distributor - CFD Preprocessing
This kind of simulation of the Pelton distributor is run in a single-phase mode. At the outlet of each of the six nozzles is a special extension that helps to stabilize the water flow throughout the outlet of the domain.
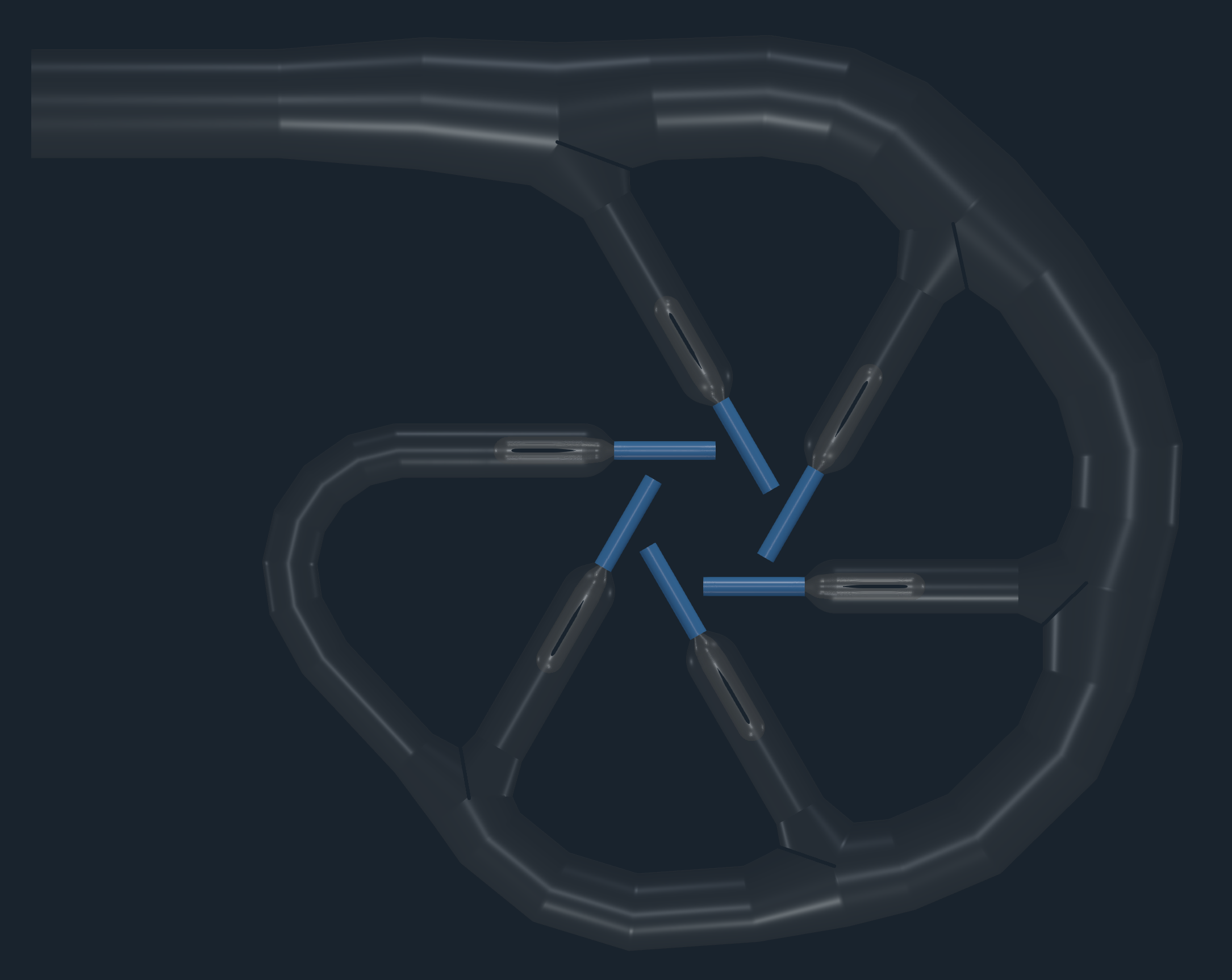
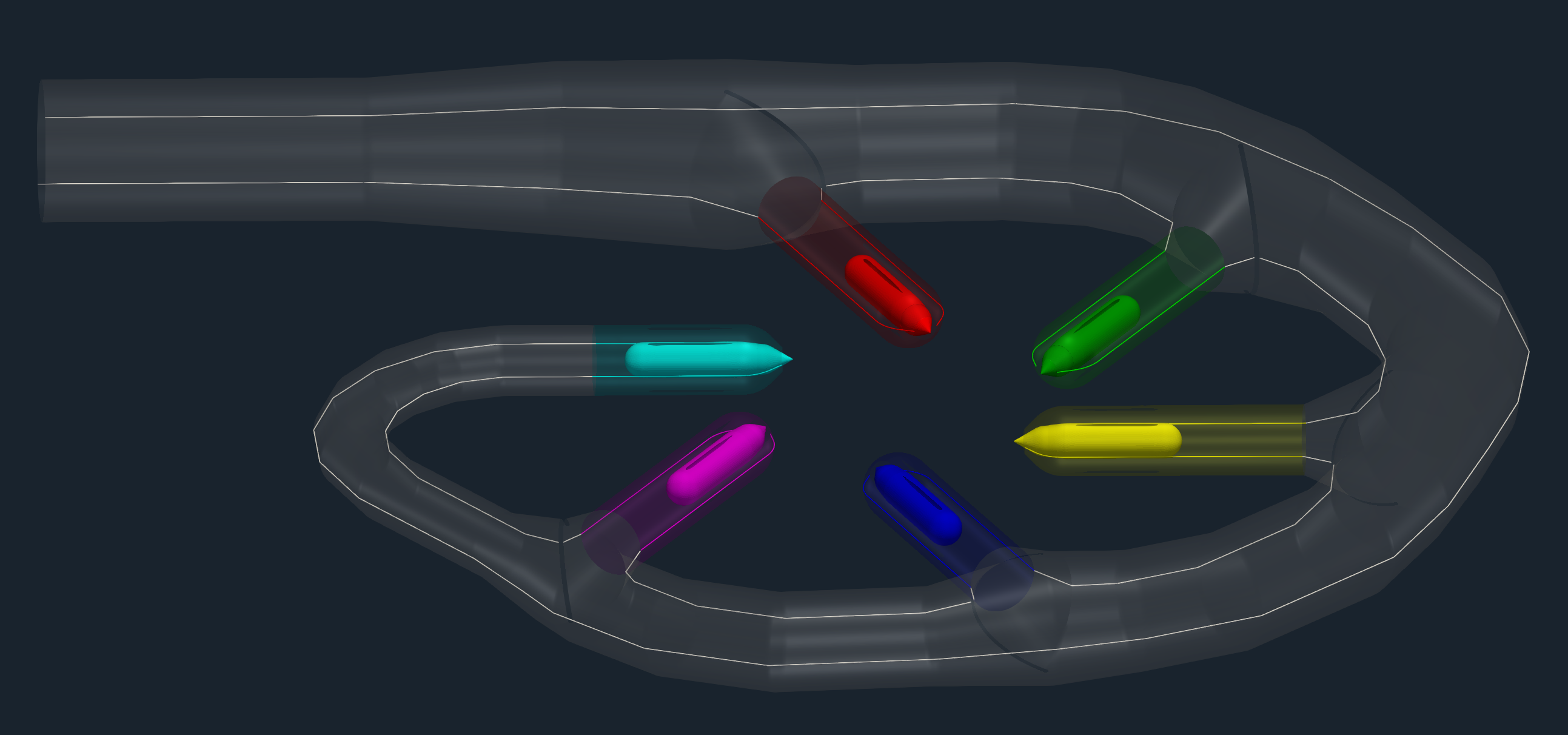
A typical input for a detailed simulation analysis is a watertight (wet) surface model in form of an STL surface. For CFD simulation, it is necessary to get a closed watertight model (sometimes called waterproof model, or model negative, or wet surface) of the CAD model inner parts where the fluid flows. For FEA simulation, it is necessary to get a closed surface model of the solid of the impeller (impeller) in form of a single one closed STL surface. The CAD model of the Pelton distributor is typically received in the STEP or IGES CAD file format. Original CAD files are usually too complex for comprehensive CFD and FEA simulations, so certain preprocessing (cleaning) CAD work is generally required. While the original CAD model for this project was simplified and cleaned using Salome open-source software, any other standard CAD system can be used instead.
The principle is always the same: the surface model has to be created; all the tiny, irrelevant, and problematic model parts must be removed, and all the holes must be sealed up (watertight surface model is required). This Pelton distributor CAD model is reasonably simple. The final surface model in the STL format is created as input for the meshing phase. This preprocessing phase of the workflow is extremely important because it determines the simulation potential and limits the CFD results. In this Pelton distributor project, the CAD model was split into four logical parts: Inlet tube, Impeller, Volute, and Draft tube. Each distributor part (model component) is watertight and includes its own inlet interface, outlet interface, and corresponding walls (wall, blade, hub, shroud, fillets, stator blades, vane blades, …). For each individual model component is created its own volume mesh first, and after that, for the simulation process, the individual meshes are merged into single one mesh by the TCAE processor.
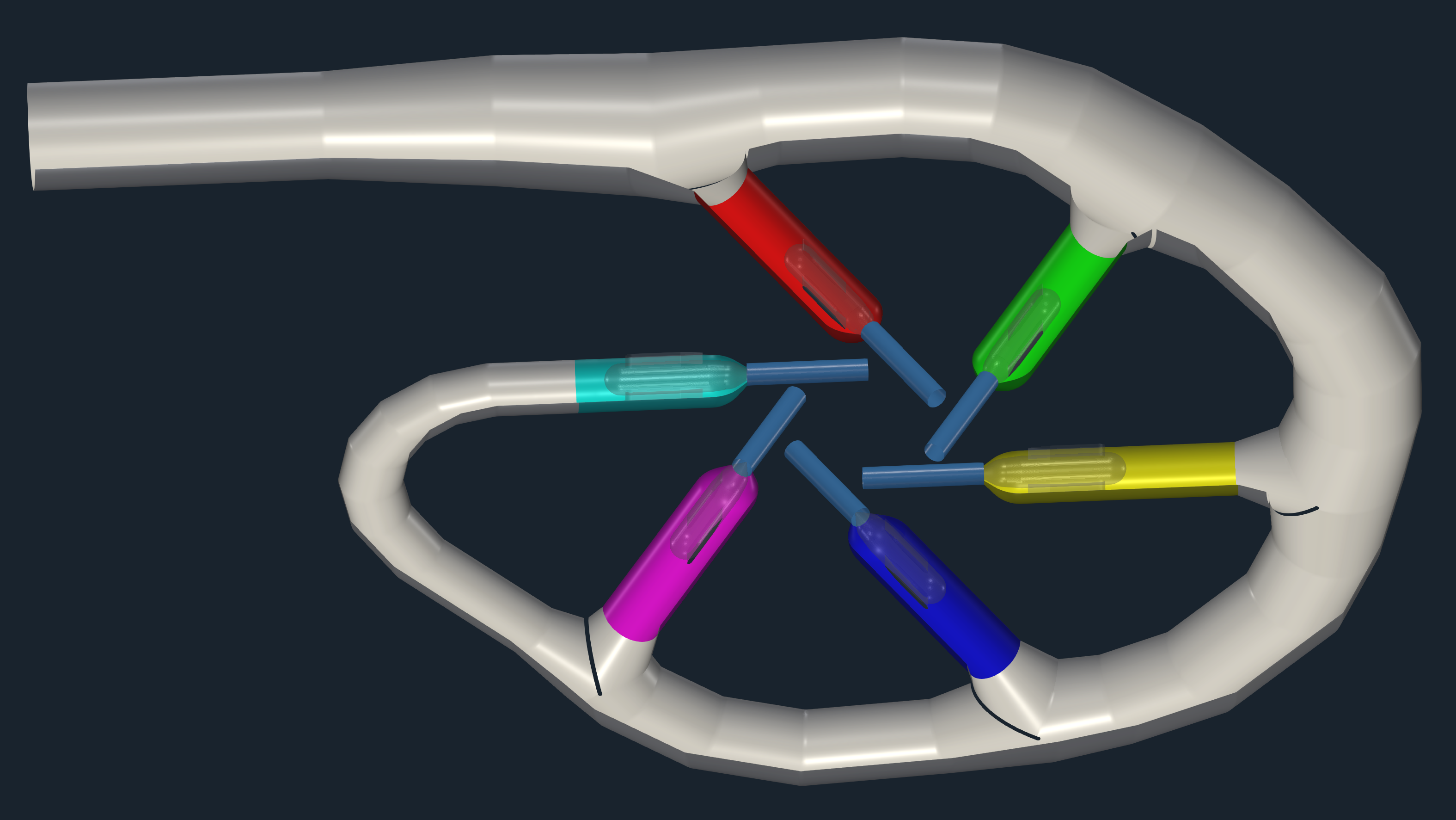
All the tiny, irrelevant, and problematic model parts must be removed, and all the holes must be sealed up. This Pelton distributor CAD model is reasonably simple. The surface model in the STL format is created as input for the meshing phase. This preprocessing phase of the workflow is extremely important because it determines the simulation potential and limits the CFD results. The surface model data in .stl file format together with physical inputs are loaded in TCFD. Other option would be loading an external mesh in OpenFOAM mesh format, or loading an MSH mesh format (Fluent mesh format), or CGNS mesh format. This CFD methodology employs a multi component approach, which means the model is split into a certain number of components. In TCFD each region can have its own mesh and individual meshes comunicate via interfaces.
IMPORTANT NOTICE
The preprocessing phase is an extremely important part of the workflow. It sets all the simulation potential and limits. It should never be underestimated. Mistakes or poor quality engineering in the preprocessing phase can be hardly compensated later in the simulation phase and postprocessing phase!!!
Pelton distributor - CFD Meshing
In this particular study, the Pelton distributor model is split into seven components. The main tube and six nozzles. Each component has its own mesh. All the meshes can be created automatically for each component within snappyHexMesh or loaded as external mesh. A combination of snappyHexMesh components and extrernal mesh components is allowed. Any number of model components (or meshes) is allowed. The computational mesh was created in an automated workflow using the snappyHexMesh application. For each model part, a cartesian block mesh was used as an initial background mesh, that is further refined. Basic mesh cell size is a cube, typically of a few milimeter edge. The mesh is gradually refined to the wall. The mesh refinement levels can be easily changed, to obtain the coarser or finer mesh, to better handle the mesh size. Inflation layers can be easily handled. The final mesh used consistes mostly of hexahedrons (approx 85%), the rest are polyhedras. The snappyHexMesh is not a compulsory meshing tool for TCAE at all. In case of need, any other external mesh can be loaded in TCAE directly in MSH, CGNS, or OpenFOAM format.
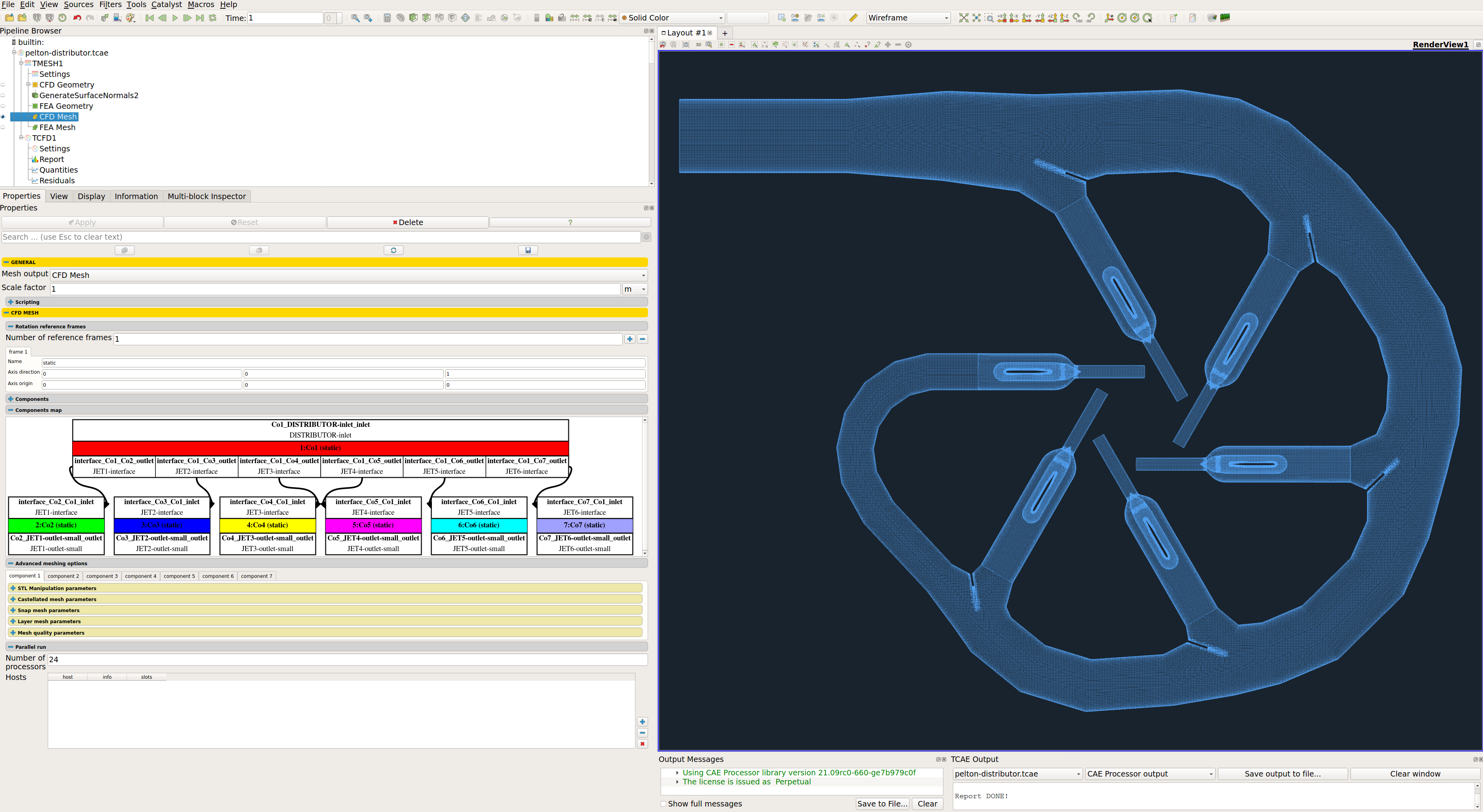
For each model component, a cartesian block mesh is created (box around the model), as an initial background mesh, that is further refined along with the simulated object. Basic mesh cell size is a cube defined with the keyword “background mesh size”. The mesh is gradually refined to the model wall. The mesh refinement levels can be easily changed, to obtain the coarser or finer mesh, to better handle the mesh size. Inflation layers can be easily handled if needed. For more details, see the TCAE documentation.
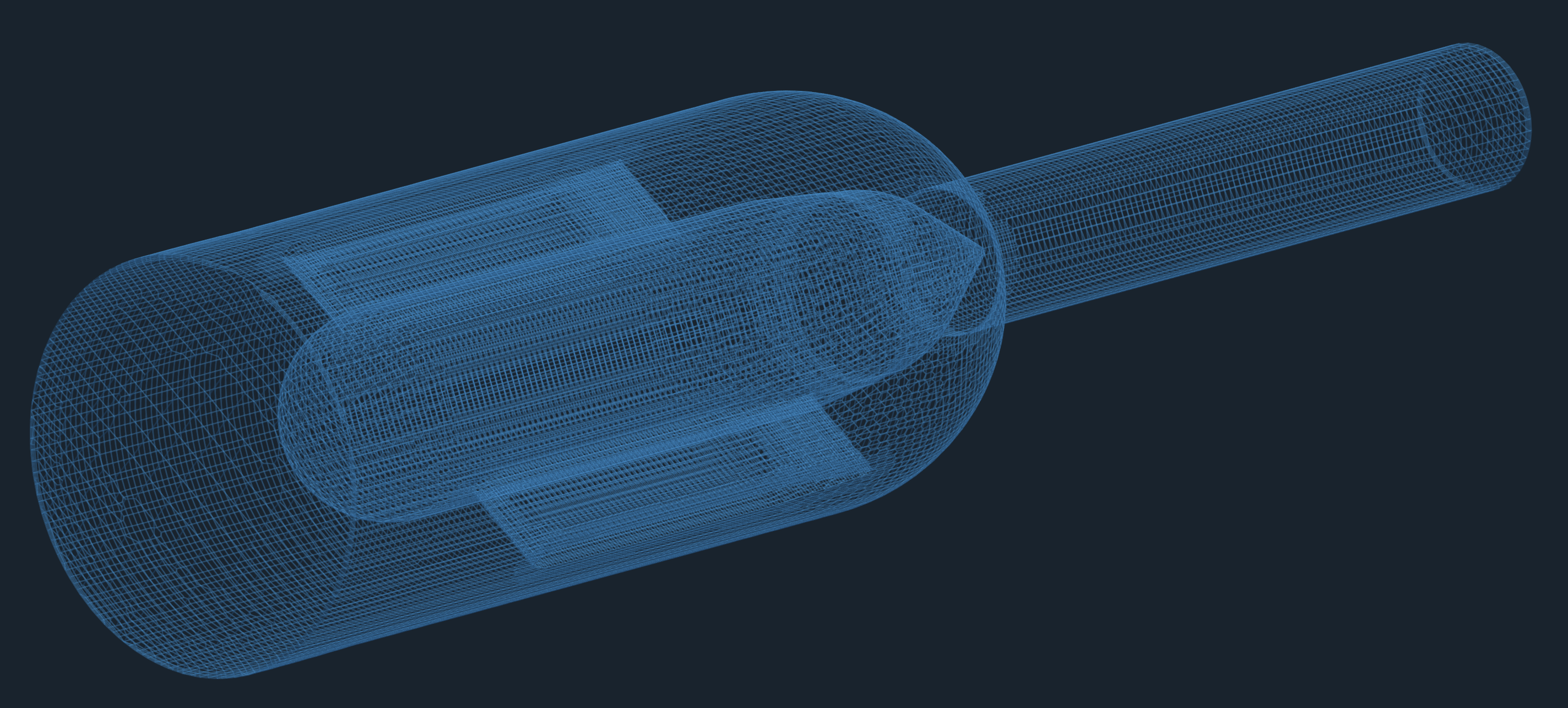
Pelton distributor - CFD Simulation Setup
The CFD simulation is managed with TCAE software module TCFD. Complete CFD simulation setup and run is done in the TCFD GUI in ParaView. TCFD uses OpenFOAM open-source application.
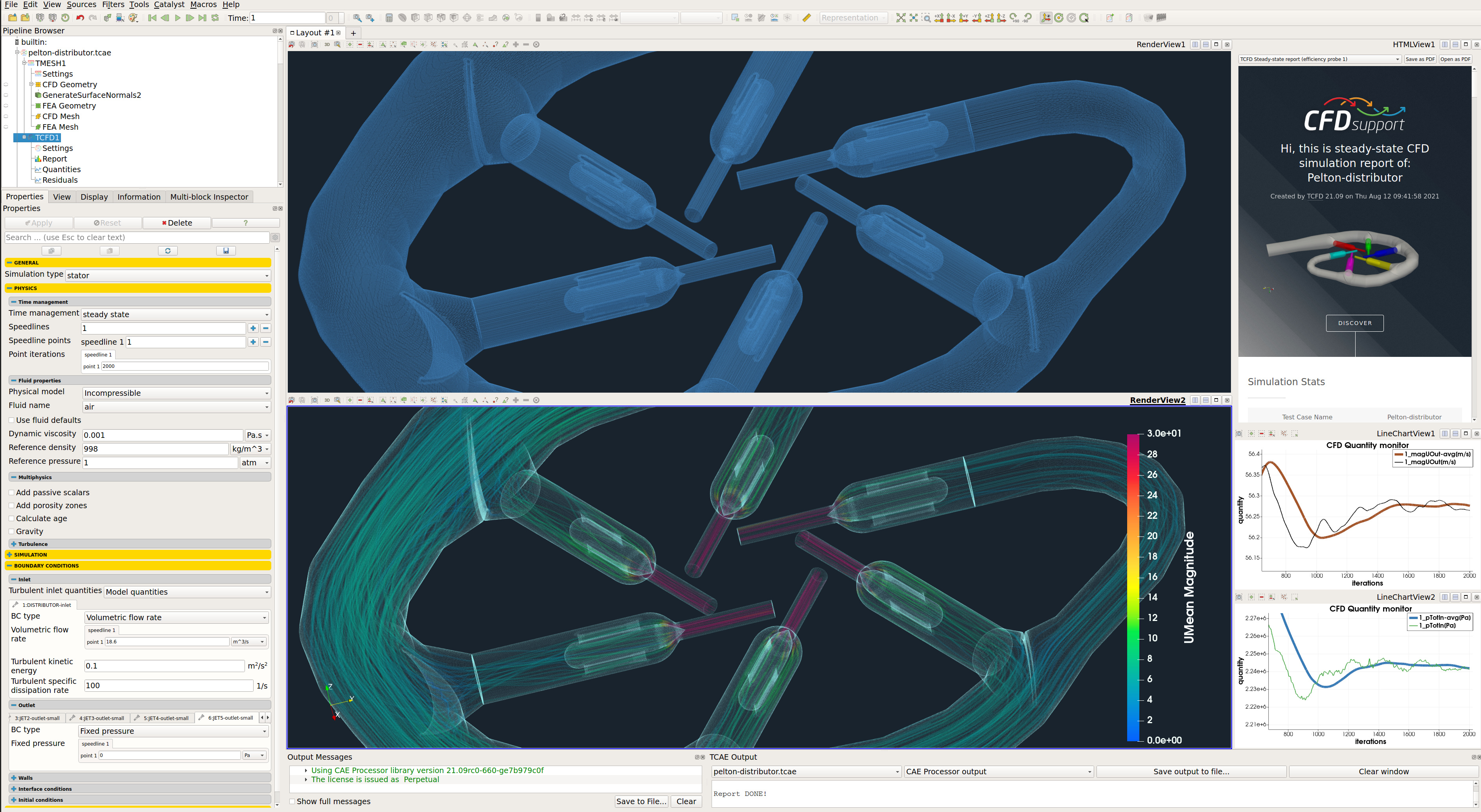
- Simulation type: Stator
- Time management: steady-state
- Physical model: Incompressible
- Number of components: 7 [-]
- Wall roughness: none
- Physical model: Incompressible
- Speed: 18.6 [m3/s]
- Outlet: Static pressure 0 [m2/s2]
- Turbulence: RANS
- Turbulence model: k-omega SST
- Wall treatment: Wall functions
- Turbulence intensity: 5%
- Speedlines: 1 [-]
- Simulation points: 7 [-]
- Fluid: Water
- Reference pressure: 1 [atm]
- Dynamic viscosity: 1.0 × 10E-3 [Pa⋅s]
- Water density: 996 [kg/m3]
- CFD CPU Time: 48 core.hours/point
- BladeToBlade: off
Any project simulated in TCFD has its component graph. The component graph shows the way the components are organized – the model topology. It shows for instance what is the inlet, the outlet and the way the components are connected via interfaces. A simple scheme of the component graph is shown below. The fluid flow enters the facility in the component Spiral via interface spiral_inflow_inlet and leaves the facility from the component drafttube via interface drafttube_outflow_outlet. This is a typical example of a very simple linear order of the flow, through a combination of three components.
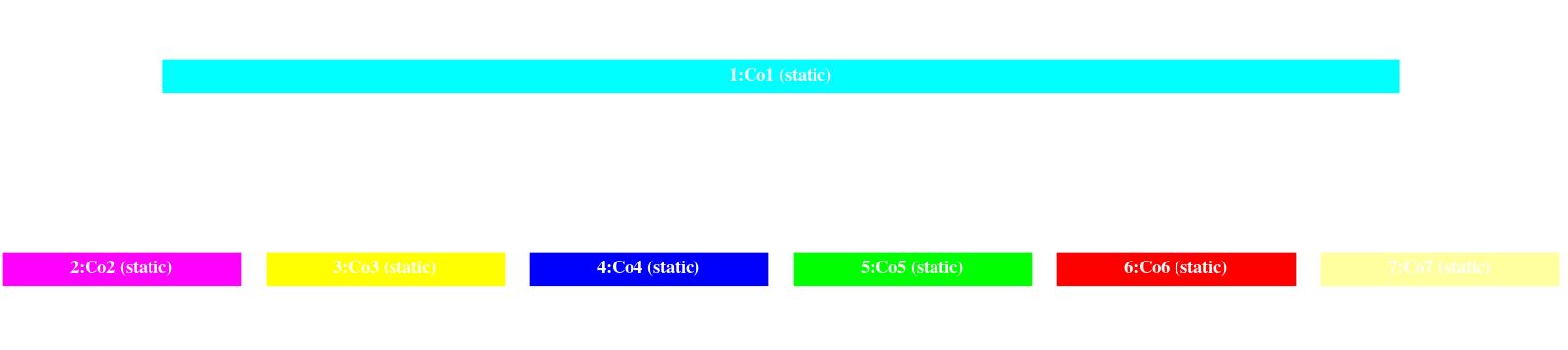
Pelton distributor - TCAE Simulation run
The TCAE simulation run is completely automated. The whole workflow can be run by a single click in the GUI, or the whole process can be run in the batch mode on a background. Modules used are TCAD, TMESH, TCFD, and TFEA. TCFD includes a built-in post-processing module that automatically evaluates all the required quantities, such as efficiency, torque, forces, force coefficients, flow rates, pressure, velocity, and much more. All these quantities are evaluated throughout the simulation run, and all the important data is summarized in an HTML report, which can be updated anytime during the simulation, for every run. All the simulation data are also saved in tabulated .csv files for further evaluation.
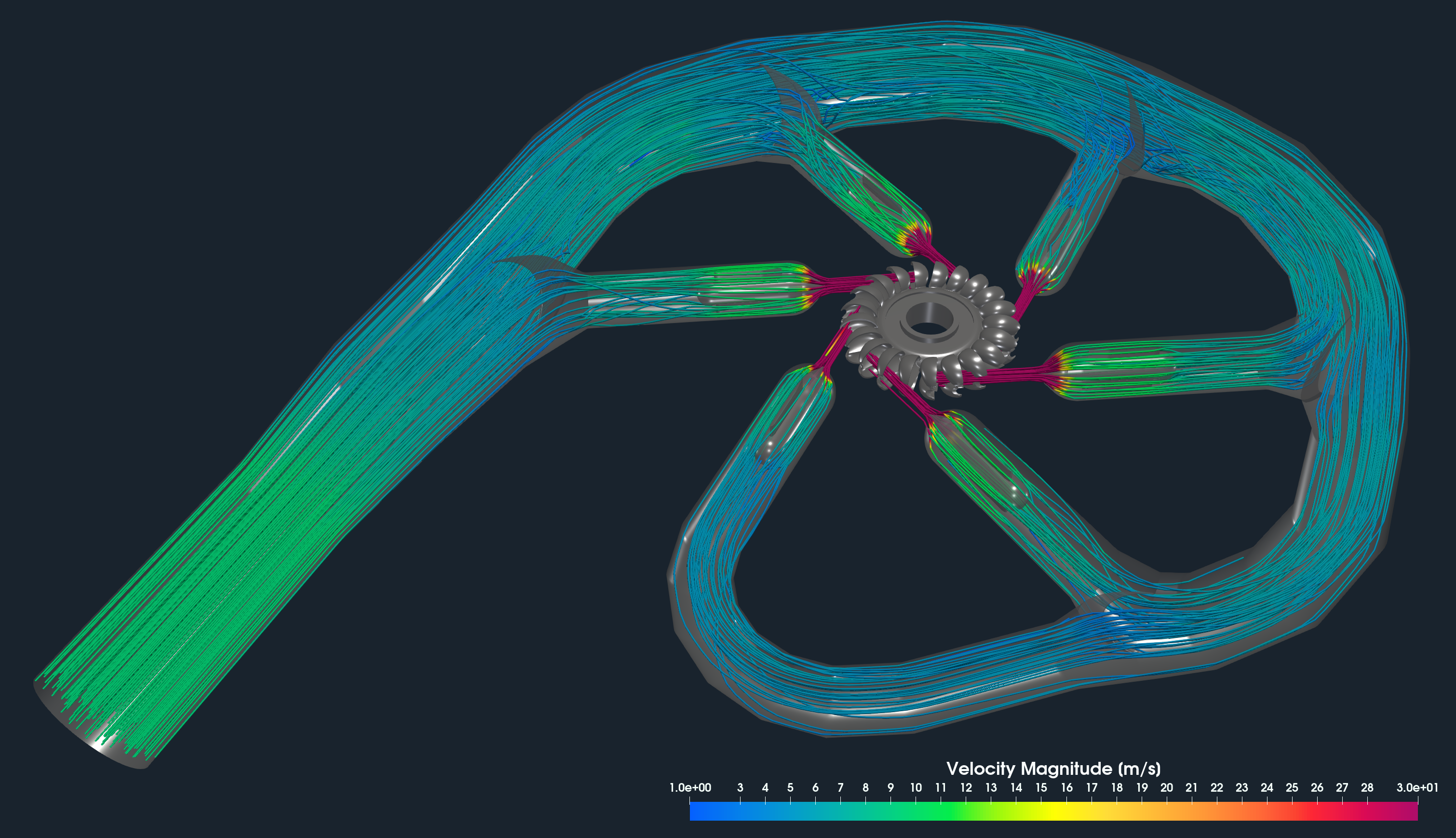
TCFD is capable of writing the results down at any time during the simulation. The convergence of basic quantities and integral quantities are monitored still during the simulation run. The geometry was created just one-time in the beginning using TCAD in the preprocessing phase. First, the TMESH is executed to create the volume meshes for CFD & FEA. Then the CFD simulation is executed and evaluated. After that, in the FSI step, the pressure field is integrated to create the force field which is prescribed as a load for the FEA simulation. Finally, the FEA simulation is executed and evaluated.
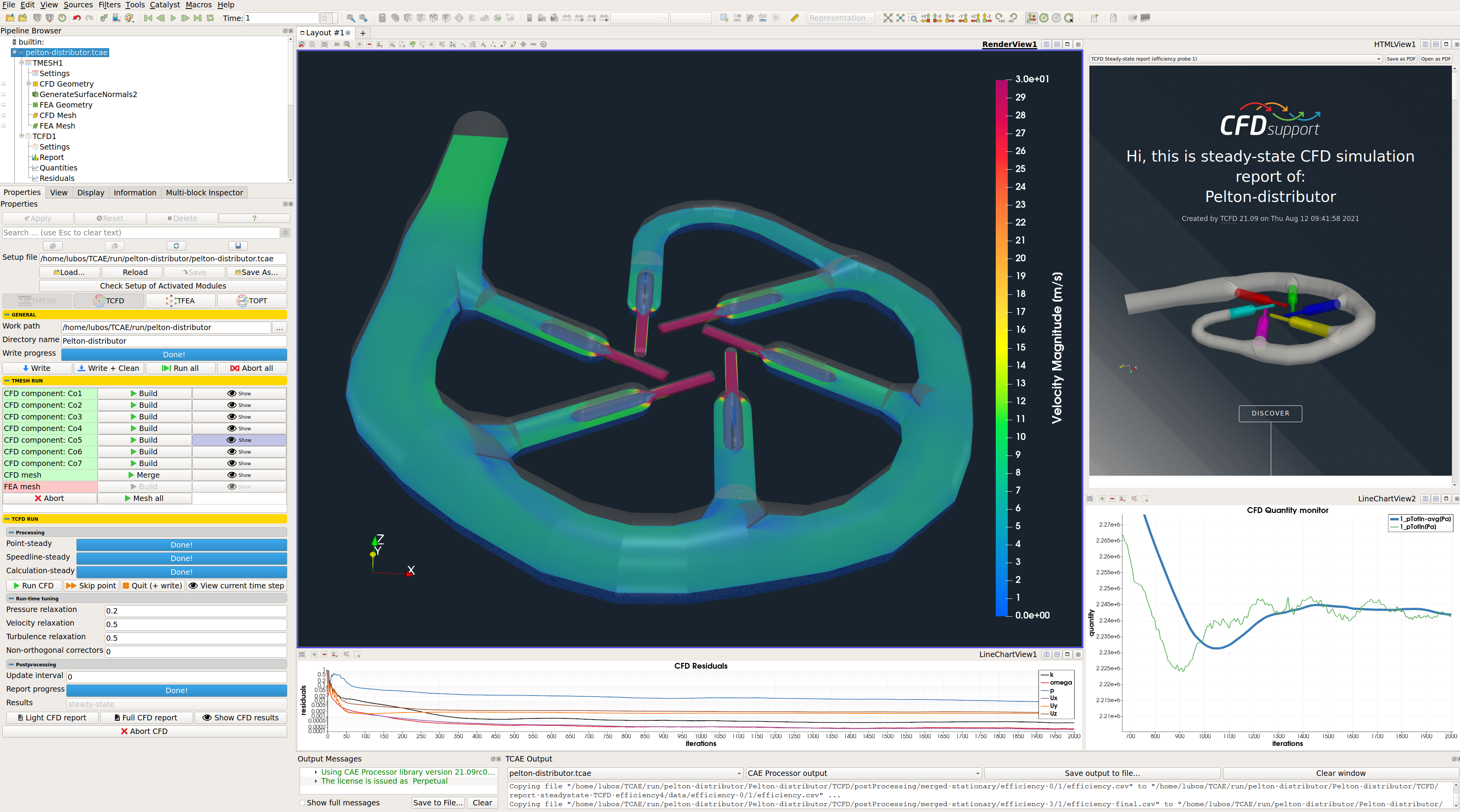
Pelton distributor - Postprocessing - Integral Results
All the integral results (efficiency, torque, head, …) are automatically evaluated and saved in the .CSV files and are available for further postprocessing if needed. The simulation results are evaluated automatically. Every simulation run in TCAE has its own unique simulation report. The integral results both for CFD and FEA are written down in the following HTML or PDF reports:
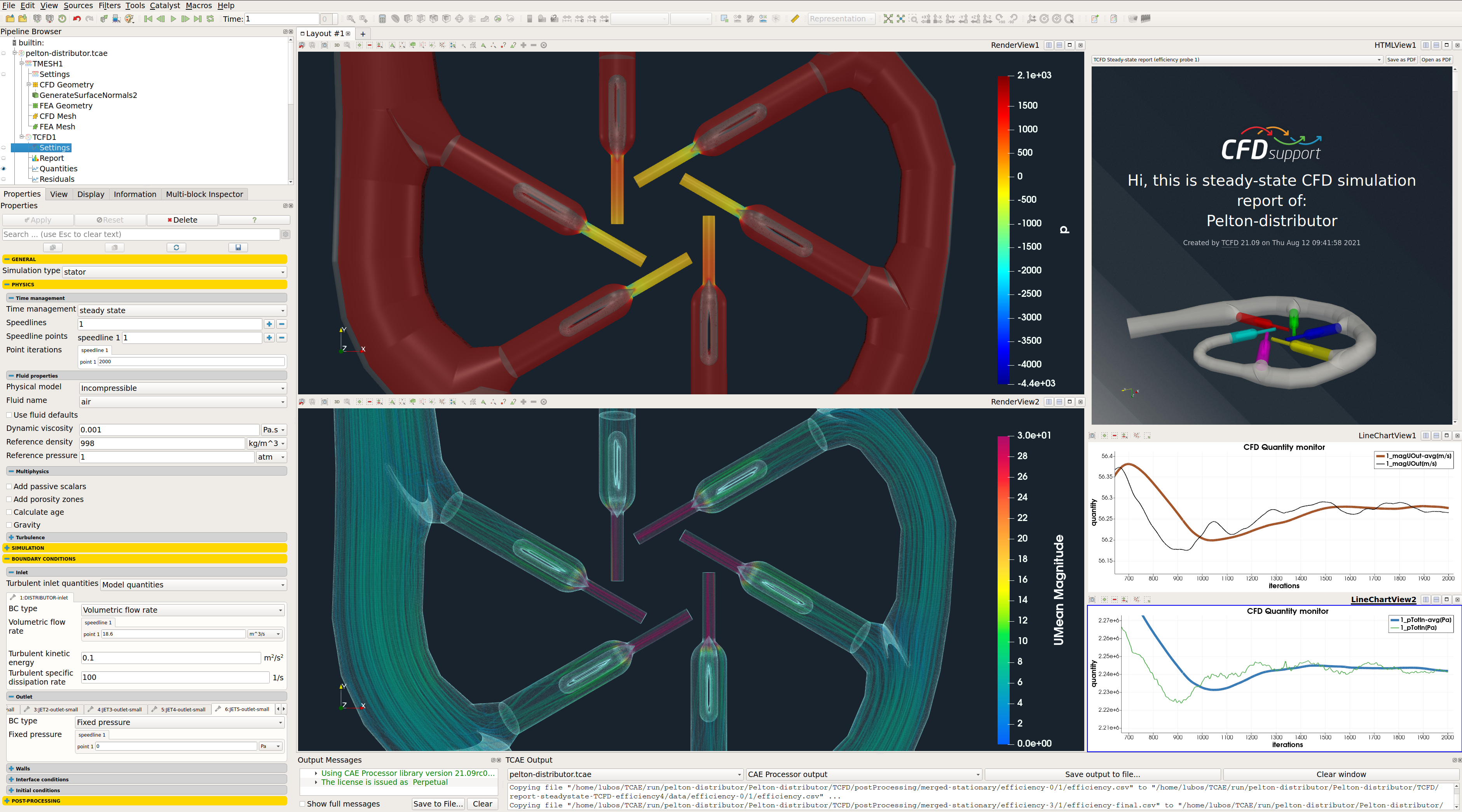
Conclusion
- It has been shown how to make a comprehensive CFD analysis of the Pelton distributor in a smooth and automated workflow.
- TCAE showed to be a very well suited tool for CFD, FEA, and FSI engineering simulations.
- More information about TCAE can be found on CFD SUPPORT website: https://www.cfdsupport.com/tcae.html
- Questions will be happily answered via email info@cfdsupport.com.
References
[1] TCAE Manual
[2] TCAE Training
[3] Wikipedia https://en.wikipedia.org/wiki/Pelton_wheel
Download TCAE Tutorial - Pelton Distributor
File name: pelton-distributor-TCAE-Tutorial-21.09.zip
File size: 20 MB
Tutorial Features: CFD, FEA, FSI, TCAE, TMESH, TCFD, TFEA, SIMULATION, FDA PUMP, RADIAL PUMP, CENTRIFUGAL PUMP, TURBOMACHINERY, INCOMPRESSIBLE FLOW, DEFORMATION, DISPLACEMENT, STRESS, MODAL ANALYSIS, INCOMPRESSIBLE, RANS, BLOOD FLOW, STEADY-STATE, AUTOMATION, WORKFLOW, RADIAL FLOW, FULL IMPELLER, SNAPPYHEXMESH, NETGEN, 3 COMPONENTS, RPM=3500, R=30mm