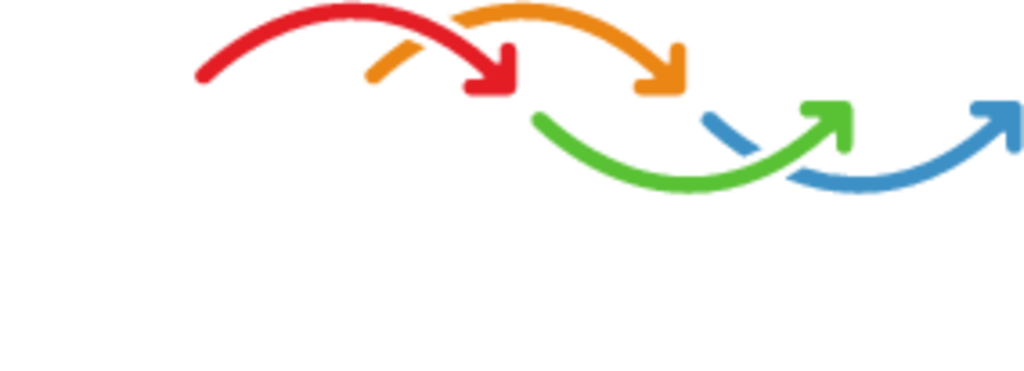
OpenFOAM® projects
OpenFOAM® projects in CFD support in general
The most common projects in CFD support company are typically those projects, where the customer wants to replace his/her current methodology based on some commercial software with OpenFOAM® methodology. Such a methodology conversion to OpenFOAM® is motivated by cost savings. Client can then decide where to spent the extra money saved on cheaper and more efficient CFD technology.
Another big group of our CFD projects is investigating some complicated physical phenomena and propose the proper solution to the customer. We call it CFD study.
Nowadays, very popular are those CFD projects which are aimed on automation of workflow connected with CFD. The CFD Process Automation is probably the biggest CFD challenge of the future leading to huge increase of productivity. The benefits are time and cost savings and elimination of human factor. The whole CFD process is automated (from preprocessing to CFD simulation and results in required data format). The new tools and methods are integrated into client’s existing PLM environments.
The last but not least group of projects is tailor-made OpenFOAM® customization. Our client simply chooses what functionality is required and we prepare it exactly according to his/her requirements.
List of past OpenFOAM® projects in CFD support
- Turbomachinery OpenFOAM® methodology
(axial turbine stages, Mixing Plane boundary condition, transonic flow, radial compressors with diffuser, radial turbines with Nozzle Guide Vane (NGV), interaction rotor – stator, frozen rotor, tailor-made postprocessing including detailed analysis of the stage)
- Full automation of CFD computations
(OpenFOAM® methodology for axial turbines, whole cfd process is automated: reading/building geometry and boundary conditions, creating computational mesh, preprocessing, running simulation, tailor-made postprocessing including evaluation of turbine stage efficiency)
- Automobile external aerodynamics
(case and computational OpenFOAM® methodology, including engine compartment flows, heat exchangers, porous zones, ventilators, MRF, advanced postprocessing, best practice set-up, whole process automated)
- Automobile external aerodynamics
(case and computational OpenFOAM® methodology, including engine compartment flows, heat exchangers, porous zones, ventilators, MRF, advanced postprocessing, best practice set-up, whole process automated)
- Turbulence models for OpenFOAM®
(RANS, DES, LES, new models implementation: v2f, transition k-w SST, EARSM)
- Water turbines OpenFOAM® methodology
(Kaplan & Francis turbine, complete methodology for designing water turbines, tailor-made postprocessing including evaluation of turbine efficiency)
- Air ventilators OpenFOAM® methodology
(automated methodology for designing air ventilators, tailor-made postprocessing including detailed ventilator analysis)
- Blood coagulation & sedimentation
(complex blood flow simulation model for OpenFOAM®, blood chemistry, blood coagulation, blood viscoelasticity, custom shear-thinning model, special boundary conditions)
- Environmental flows
(wind acting on buildings, forces & momentum, toxic exhausts sedimentation, critical places location)
- Flows with heat transfer
(heat exchangers, increasing efficiency)
- Variable density flows
(atmospheric flows & natural convection)
- Multiphase flows
(icing on aircrafts, sedimentation of exhausts, mixture flows, filling of car petrol tank)
- Combustion simulations
(combustion chamber flows in aircraft engine)
- Fluid structure interaction simulations
(interaction between fluid and rigid body)
- Pipeline system shape optimization
(pressure losses optimization, Adjoint method, DOE)
Please contact us for further information.
PARTNERS
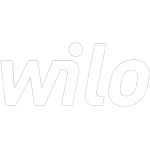
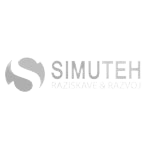
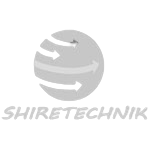
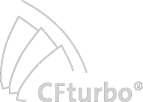
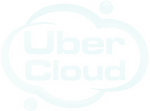
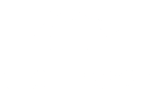
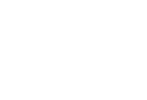
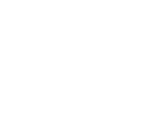
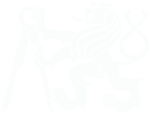
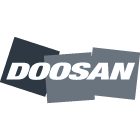
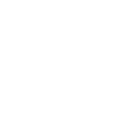
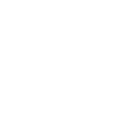
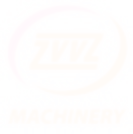
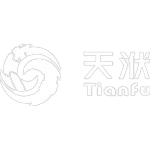
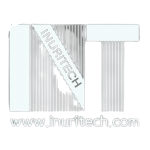
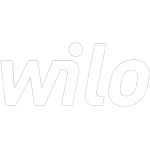
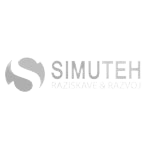
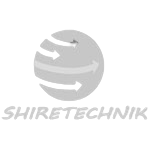
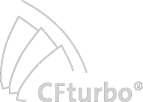
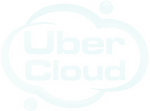
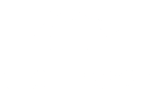