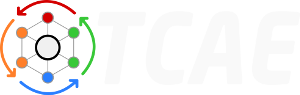
Centrifugal Fan Design and Simulation
This case study shows a complex CFD and FEA + FSI analysis of centrifugal fan using simulation environment TCAE
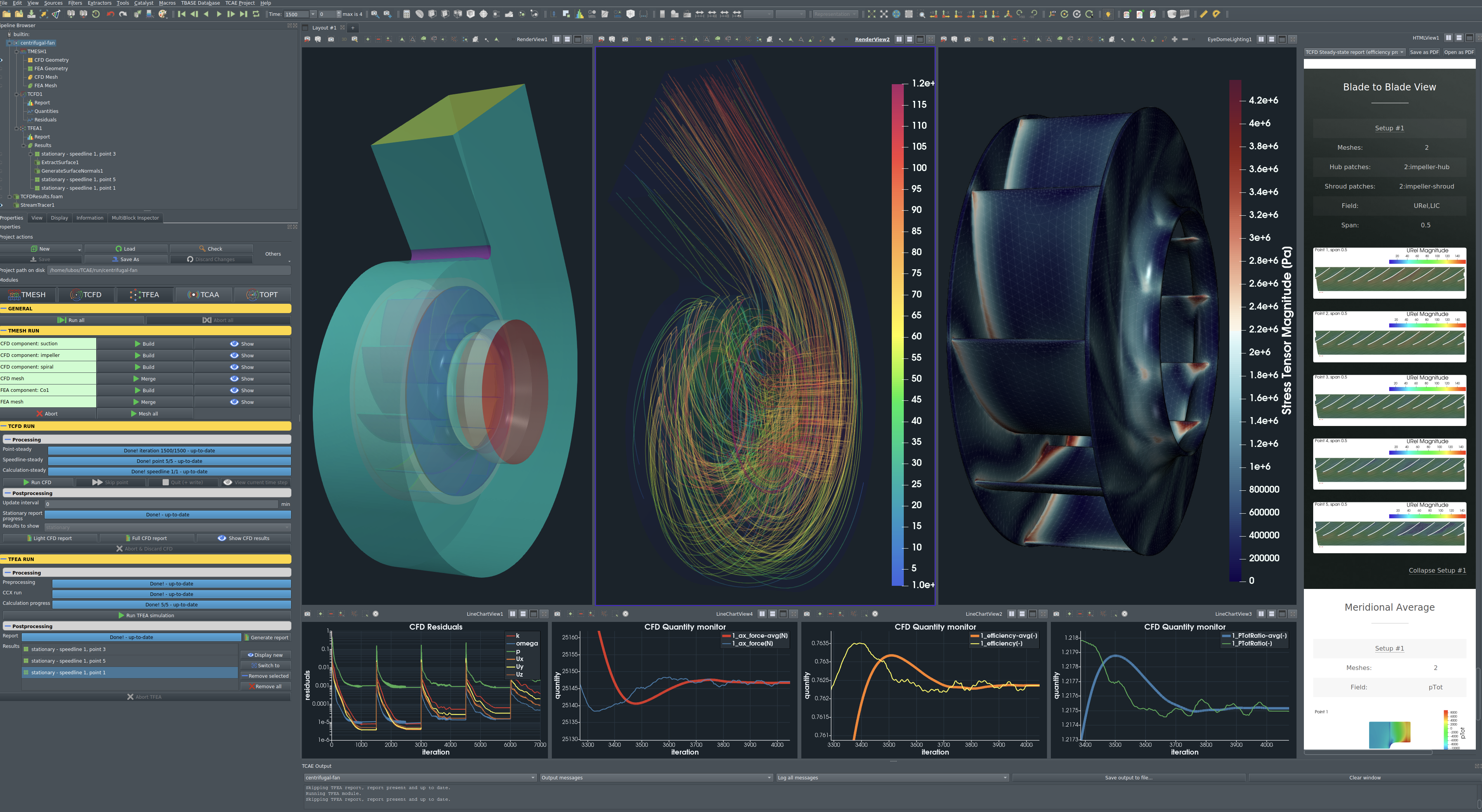
Introduction
Centrifugal fan design and simulation is a complex task. This study shows a complex step-by-step analysis of a centrifugal fan from its design to an advanced CFD & FEA simulation, including FSI and modal analysis. The simulation software used for this analysis is TCAE – a comprehensive simulation environment based on open-source. This particular centrifugal fan which is used in this example is completely artificial, however, it was derived from a real existing fan, for which the comparison of the CFD and FEA results with measurement has been made. The goal of this study is to show in detail how to make a comprehensive analysis of the basic centrifugal fan characteristics: efficiency, phi-psi, torque, power, pressure, stress, displacement, modal analysis, and many more.
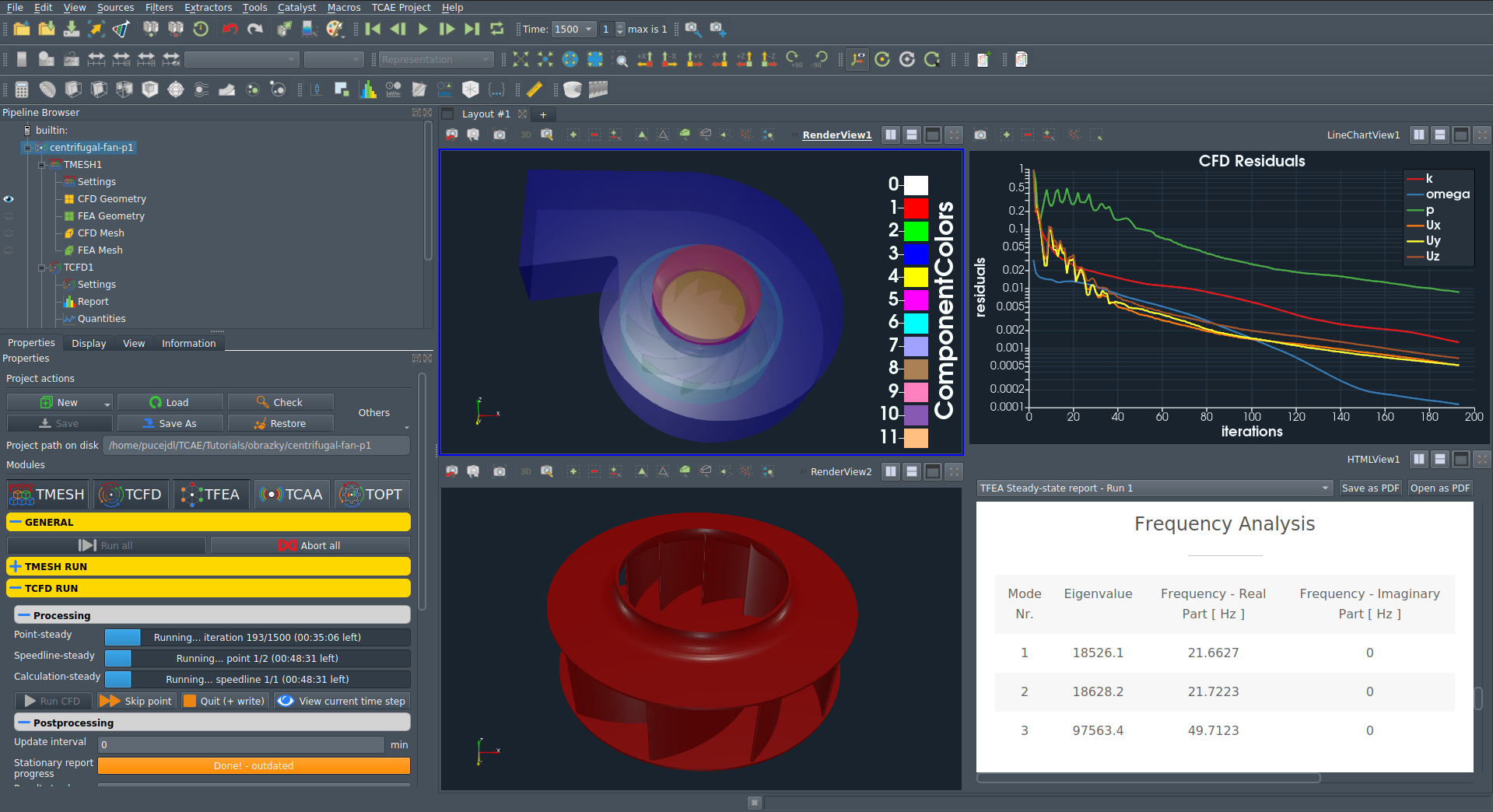
Centrifugal Fan Design
A typical input for a detailed simulation analysis is a watertight (wet) surface model in form of STL surface. For CFD simulation, it is needed to have a closed watertight model (sometimes called waterproof, or model negative, or wet surface) of the fan inner parts where the air flows. For FEA simulation, it is needed to have a closed surface model of solid of the impeller in form of a single one STL surface.
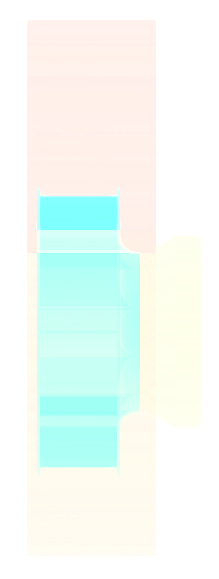
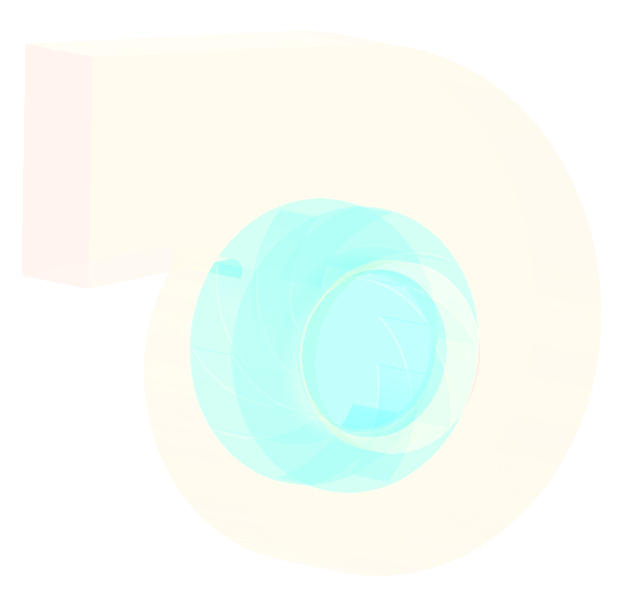
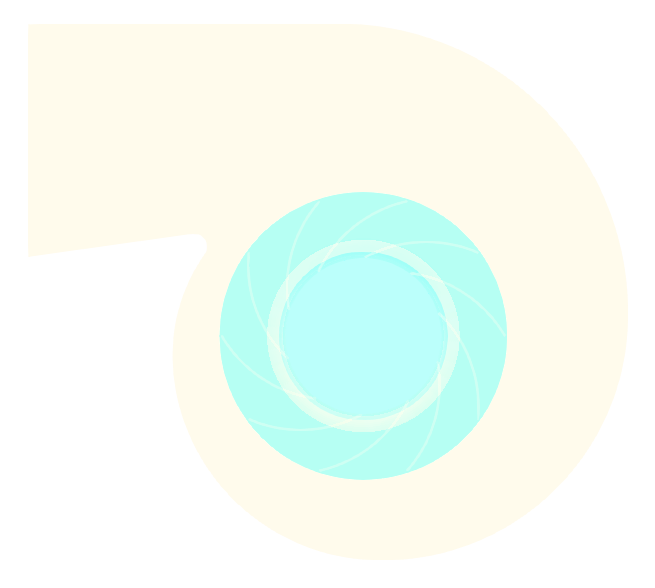
This study shows a complex step-by-step analysis of a centrifugal fan from its design to an advanced CFD & FEA simulation, including FSI and modal analysis. The simulation software used for this analysis is TCAE – a comprehensive simulation environment based on open-source. This particular centrifugal fan which is used in this example is completely artificial, however, it was derived from a real existing fan, for which the comparison of the CFD and FEA results with measurement has been made. The goal of this study is to show in detail how to make a comprehensive analysis of the basic centrifugal fan characteristics: efficiency, phi-psi, torque, power, pressure, stress, displacement, modal analysis, and many more.
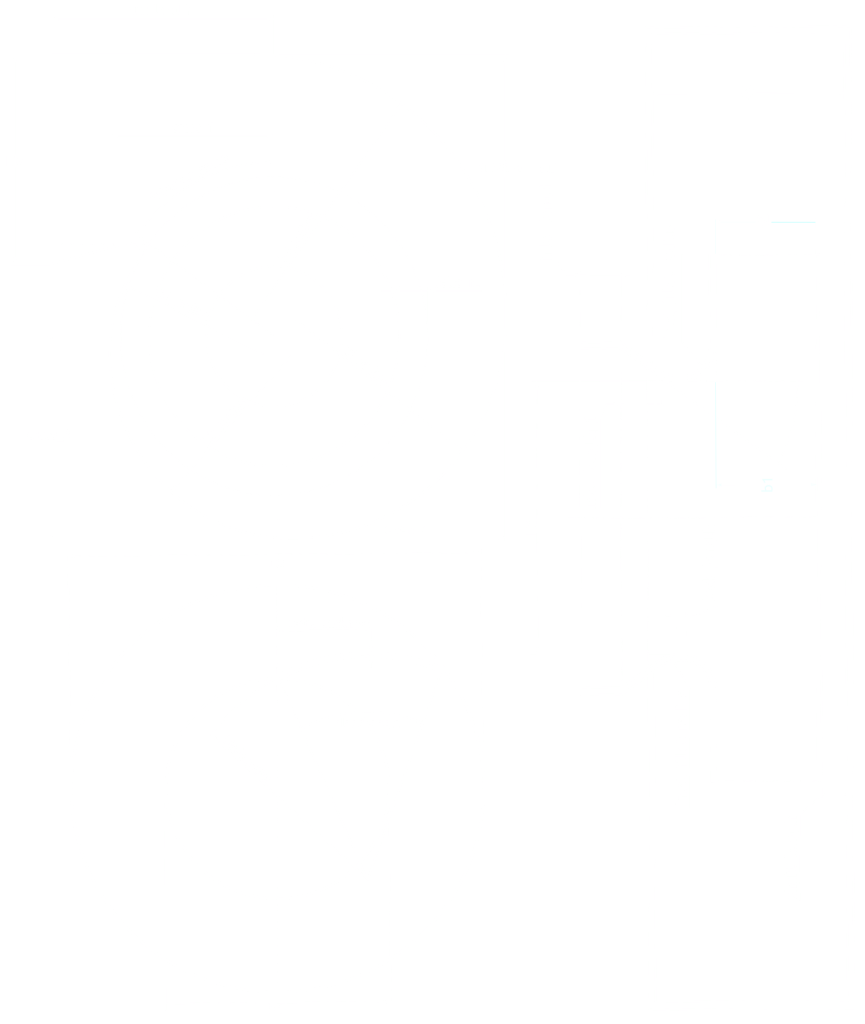
CFDSUPPORT has developed a special geometry builder for centrifugal fans, based on Salome, inside TCAE software module TCAD. This centrifugal fan TCAD geometry builder reads the set of parameters and creates the CAD geometry in the STEP format, and extracts the STL surface out of it. STL surface is needed for the CFD & FEA simulation. For example, consider the following centrifugal fan parameters:
D1=0.6
blade_angle = math.radians(29.0)
spiral = True
cross_1 = 0.732
k2_radius = 0.802
inlet_length_2 = 0.100
D2 = 1.100
b2 = 0.3
BS = 0.5
cross_2 = 0.863
k3_radius = 0.946
inlet_fillet_radius = 0.077
blade_radius = 0.5
b1 = 0.3
TR = 0.05
cross_3 = 1.018
k4_radius = 1.116
inlet_angle = math.radians(32)
blade_thickness = 0.01
shaft_length = 0.04
HV = 0.9
cross_4 = 1.201
out_length = 1.2
opennes_angle = math.radians(55)
number_of_blades = 10
impeller_solid_thickness = 0.010
delta_rz = 0.138
k1_radius = 0.680
inlet_length_1 = 0.743/2
lock_length = 0.010
Such combination of parameters leads to the following centrifugal fan geometry:

Centrifugal Fan - CFD Preprocessing
For CFD simulation it is best to split the centrifugal fan into several waterproof components because of rotation (some parts are rotating and some parts are not). Each component consists of a few or multiple STL surfaces. It is smart to split the surface model into multiple surfaces because it opens a wider range of simulation methods (mesh refinements, manipulation, boundary conditions, evaluation of results on model parts, …). This particular centrifugal fan seems reasonable to be split into three components: Spiral, Impeller, and Suction.
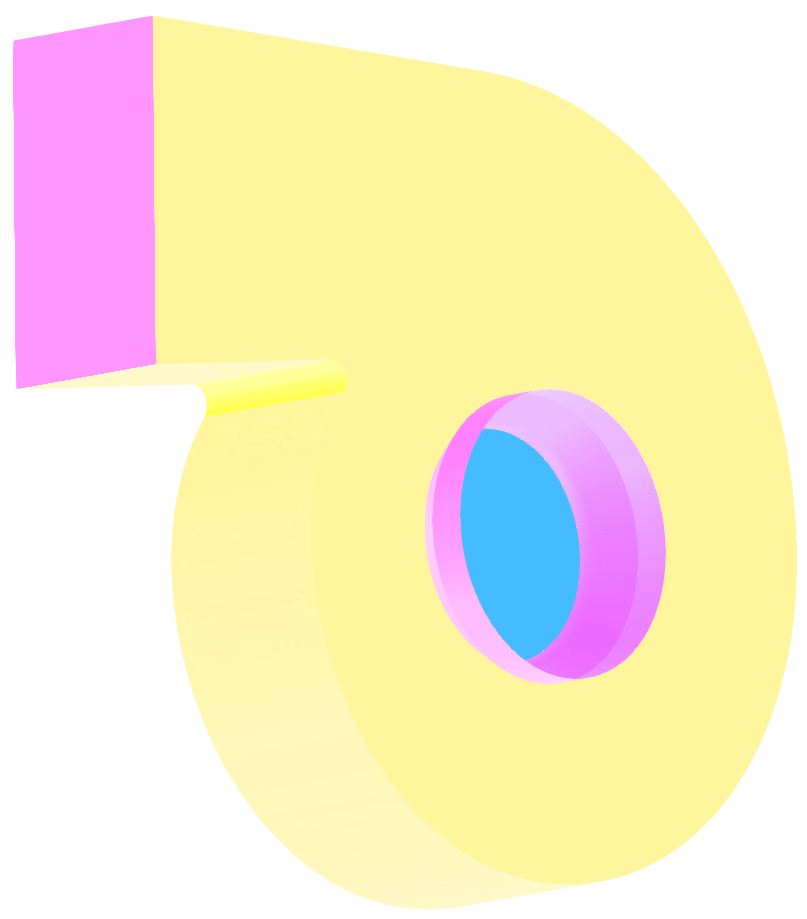
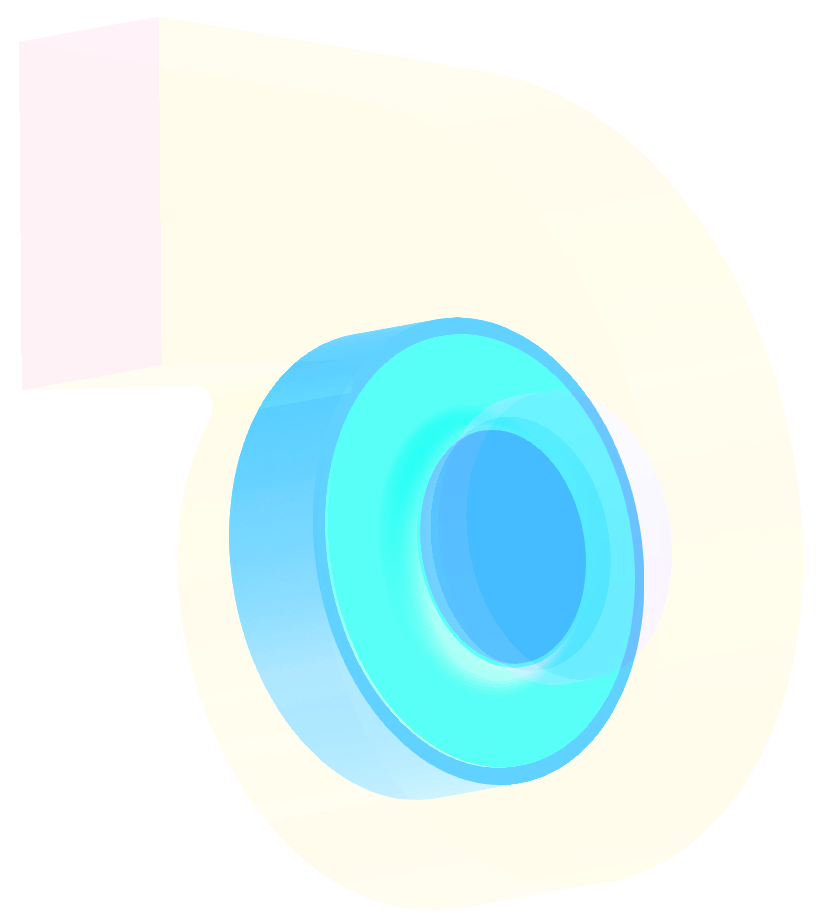
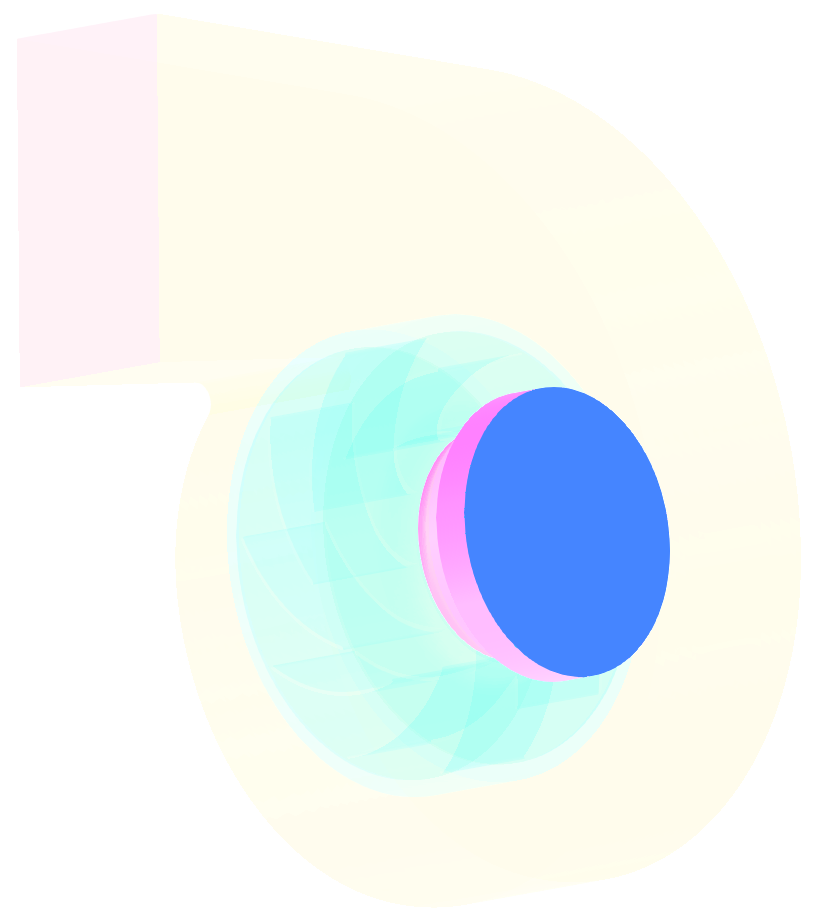
The model topology is always up to the user, there are no limitations on the number of components or individual surfaces. In any case, the final model for CFD simulation needs to be split into closed waterproof components. This centrifugal fan is split into three components. First one is called suction. The second one is called impeller (this component is rotating). The third component is called spiral. The following image shows the meridional view of the centrifugal fan split into three components:
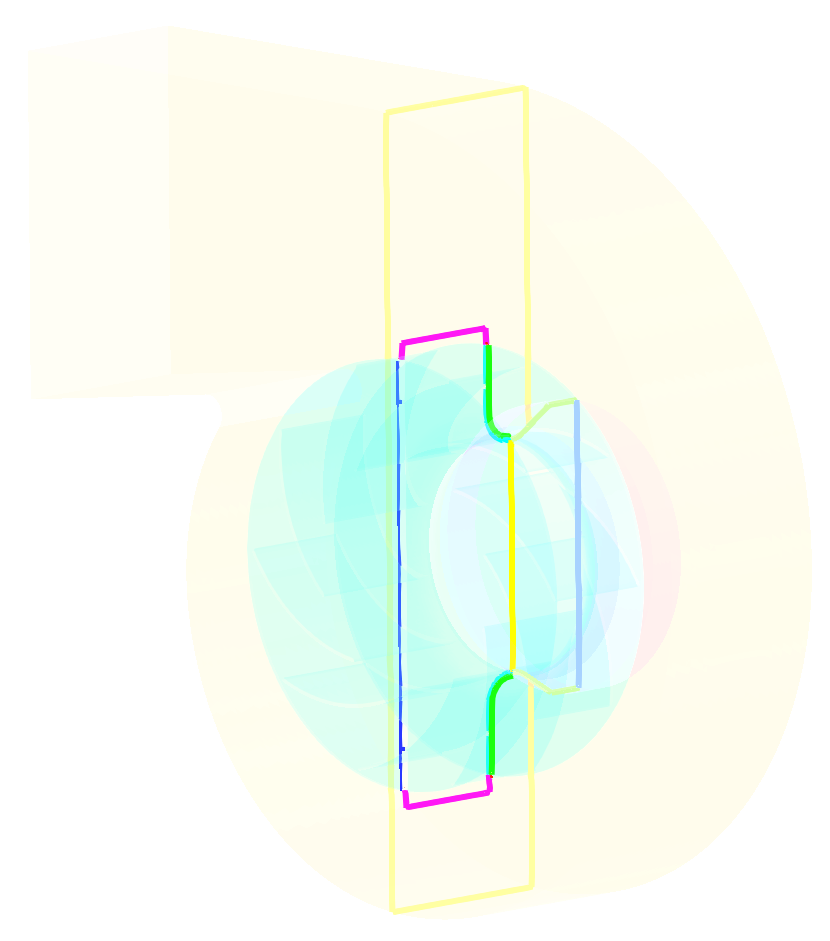
Each component consists of individual STL files. Typically, they are the inlet, the outlet, and the wall. For example, within a simplest possible approach, the impeller component can consist just out of three STL surfaces called, for instance:
impeller-inlet.stl
impeller-outlet.stl
impeller-wall.stl
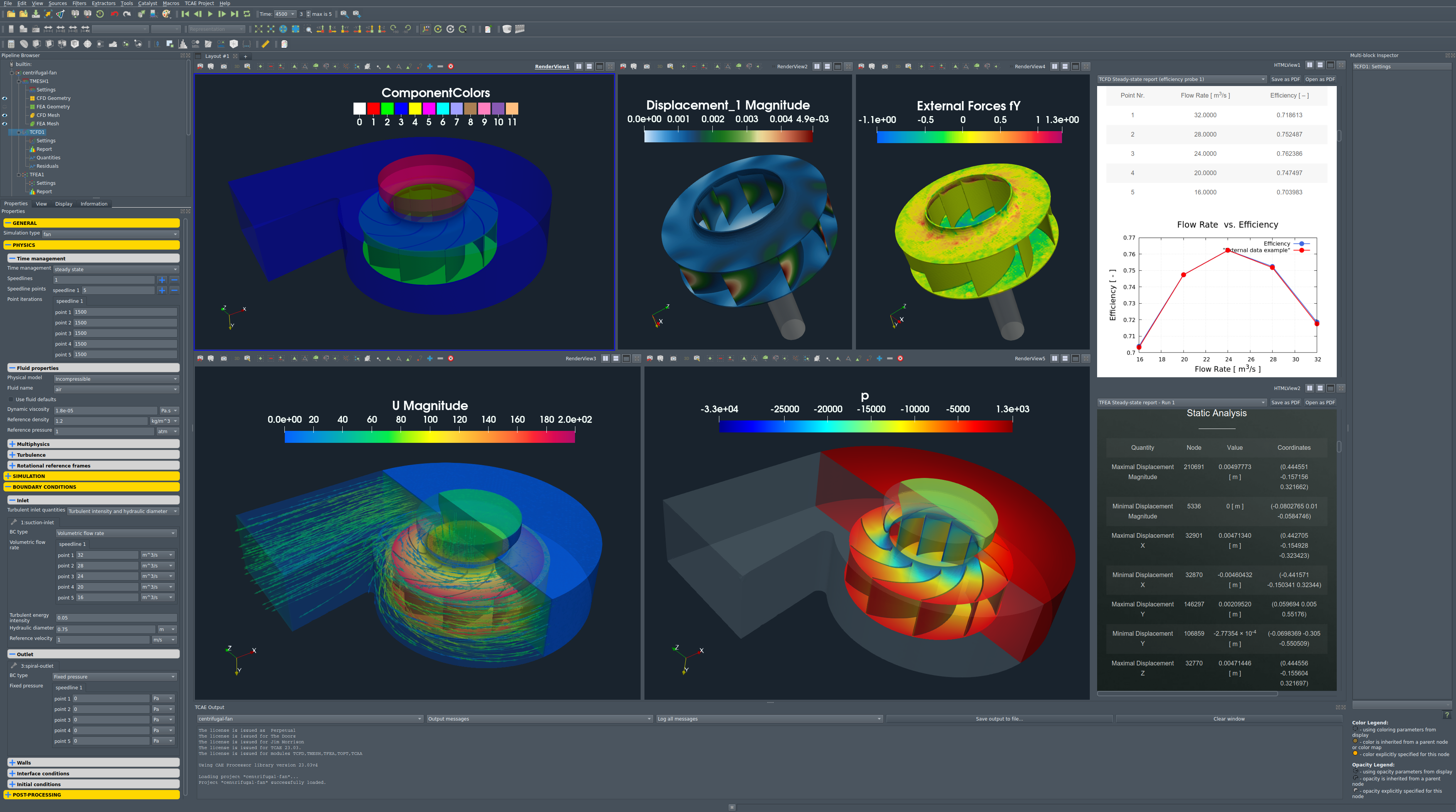
Or, within a detailed approach, the impeller component can consist out of the following parts:
Impeller.intel.stl
impeller-outlet-shroud.stl
Impeller-outlet.stl
Impeller-blade-pressure-side.stl
Impeller-inner-hub.stl
Impeller-blade-suction-side.stl
impeller-inner-shroud.stl
impeller-blade-leading-edge.stl
impeller-outer-hub.stl
impeller-blade-trailing-edge.stl
Impeller-hubShroud-leading-edge.stl
impeller-hubShroud-trailing-edge.stl
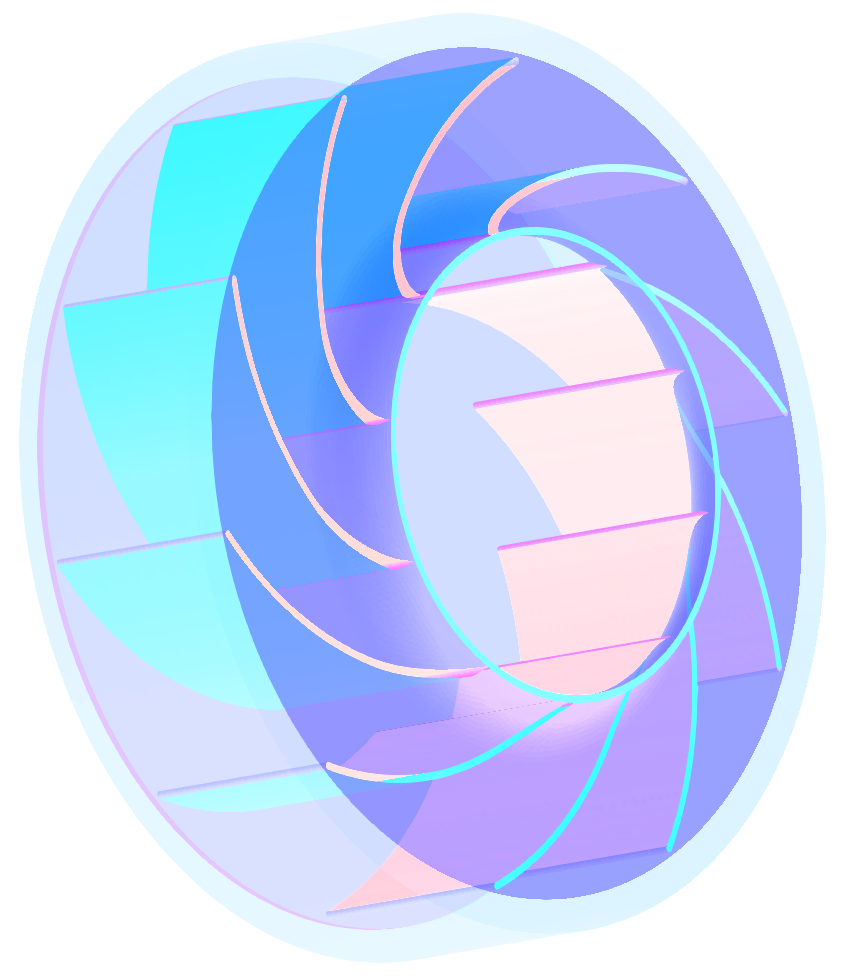
Such structure of surface files allows much more possibilities for performing high tech simulations (mesh refinements, manipulation, boundary conditions, evaluation of results on model parts, …). On the other hand, a simple structure if often sufficient and easier for simulation setup. For more details, see the TCAE documentation. Now the CFD model is ready for meshing with TMESH using snappyHexMesh open-source application.
Centrifugal Fan - FEA Preprocessing
For FEA simulation, it is best to create a simple, single one, closed STL surface of the centrifugal impeller solid, for instance impeller-solid.stl. That has already been created with the TCAD geometry builder in the design stage.
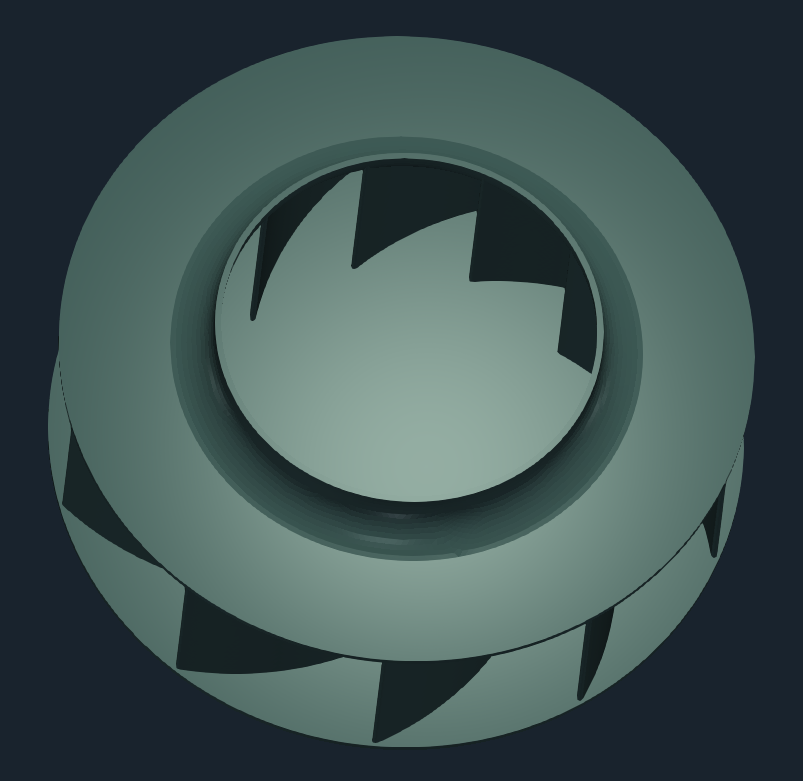
Centrifugal Fan - CFD Meshing
The computational mesh for CFD is created in an automated software module TMESH, using the snappyHexMesh open-source application. All the mesh settings are done in the TCAE GUI.
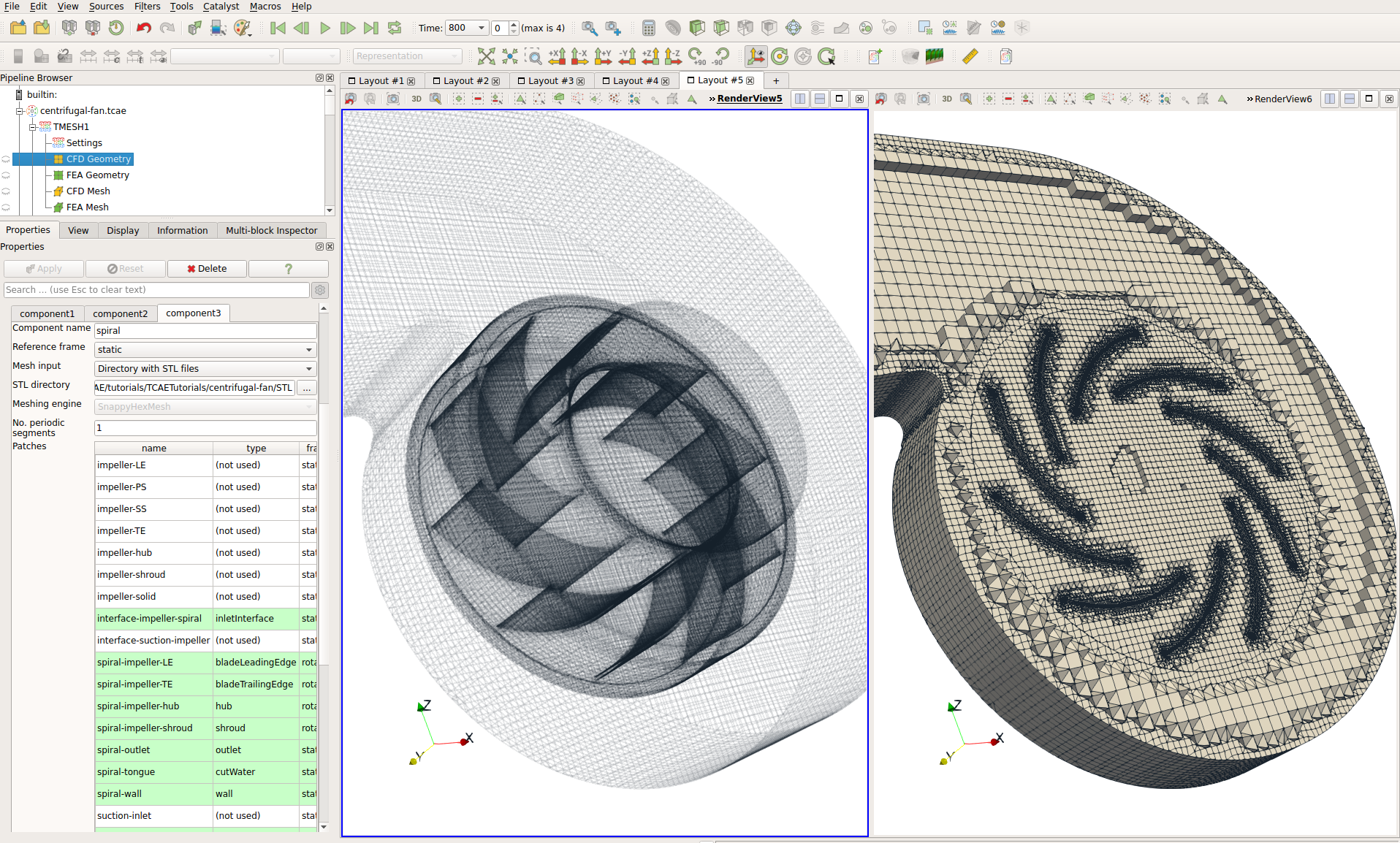
For each model component, a cartesian block mesh is created (box around the model), as an initial background mesh, that is further refined along with the simulated object. Basic mesh cell size is a cube defined with keyword “background mesh size”. The mesh is gradually refined to the model wall. The mesh refinement levels can be easily changed, to obtain the coarser or finer mesh, to better handle the mesh size. Inflation layers can be easily handled if needed. For more details, see the TCAE documentation.
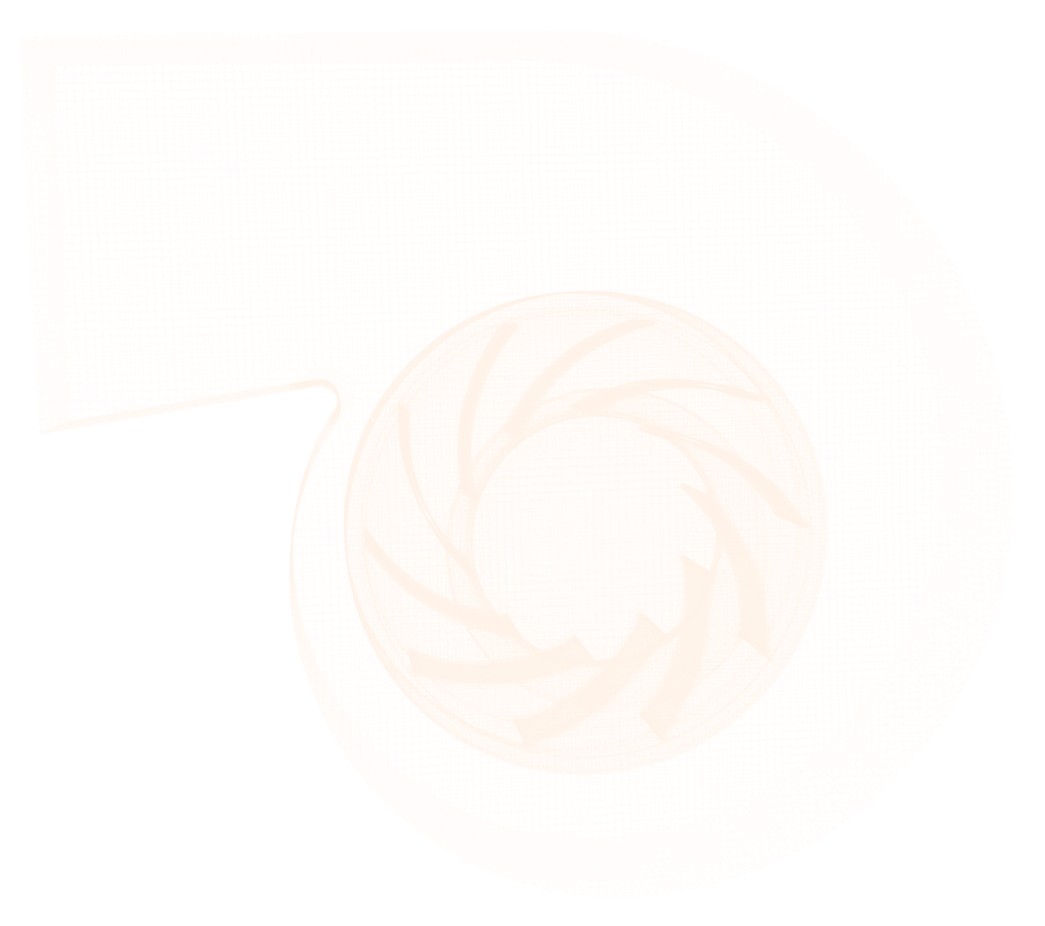
Centrifugal Fan - FEA Meshing
The computational mesh for FEA is created in an automated software module TMESH, using the NetGen open-source application. All the mesh settings are done in the TCAE GUI.
The computational mesh for FEA is created in an automated software module TMESH, using the NetGen open-source application. All the mesh settings are done in the TCAE GUI.
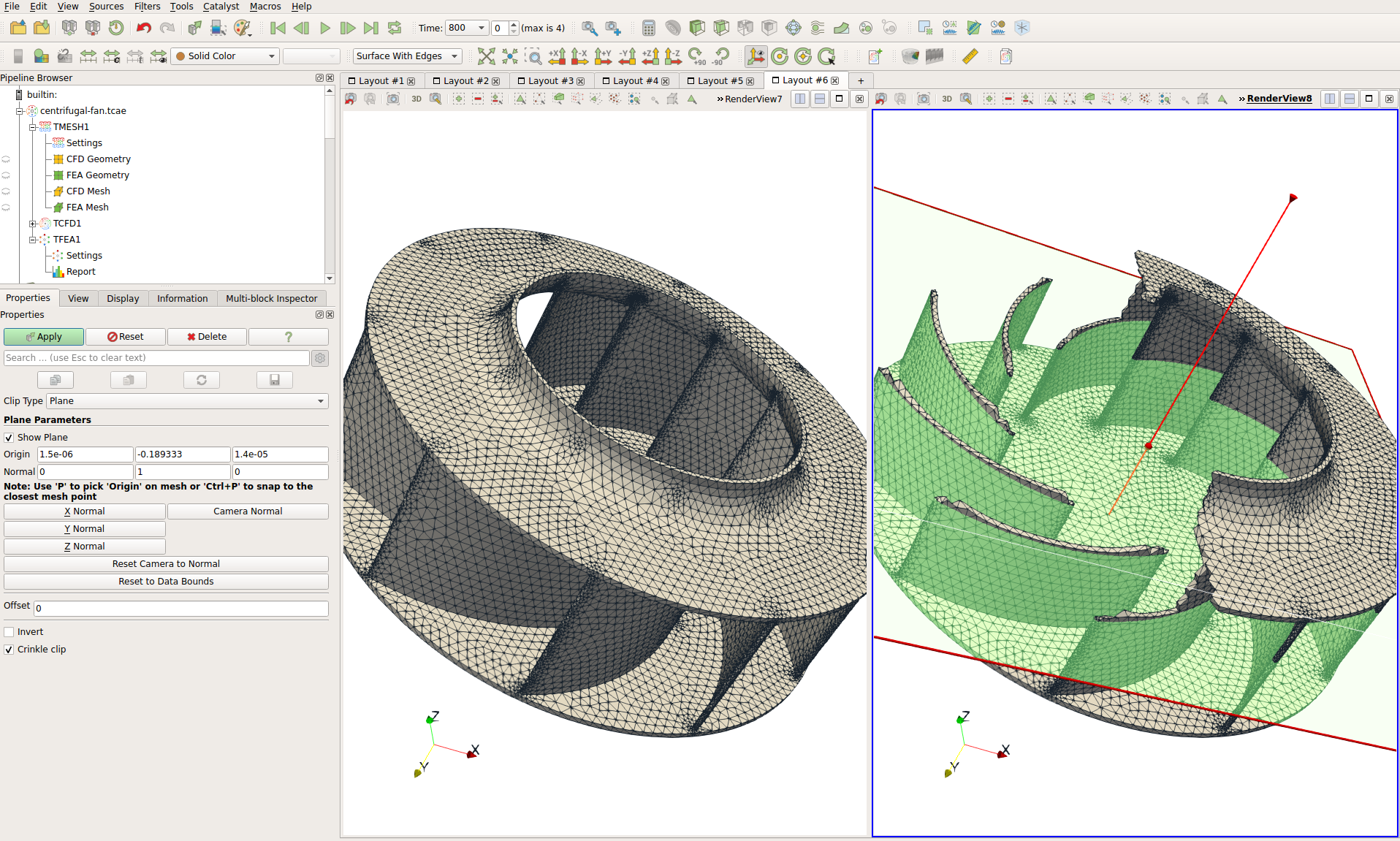
The closed STL model is meshed with just a little effort because there are just a few parameters to set. The most important parameters for FEA meshing are “h Max” and “h Min” which mean the maximal and minimal mesh edge in meters. The mesh is created with an automated algorithm. For more details, see the TCAE documentation.
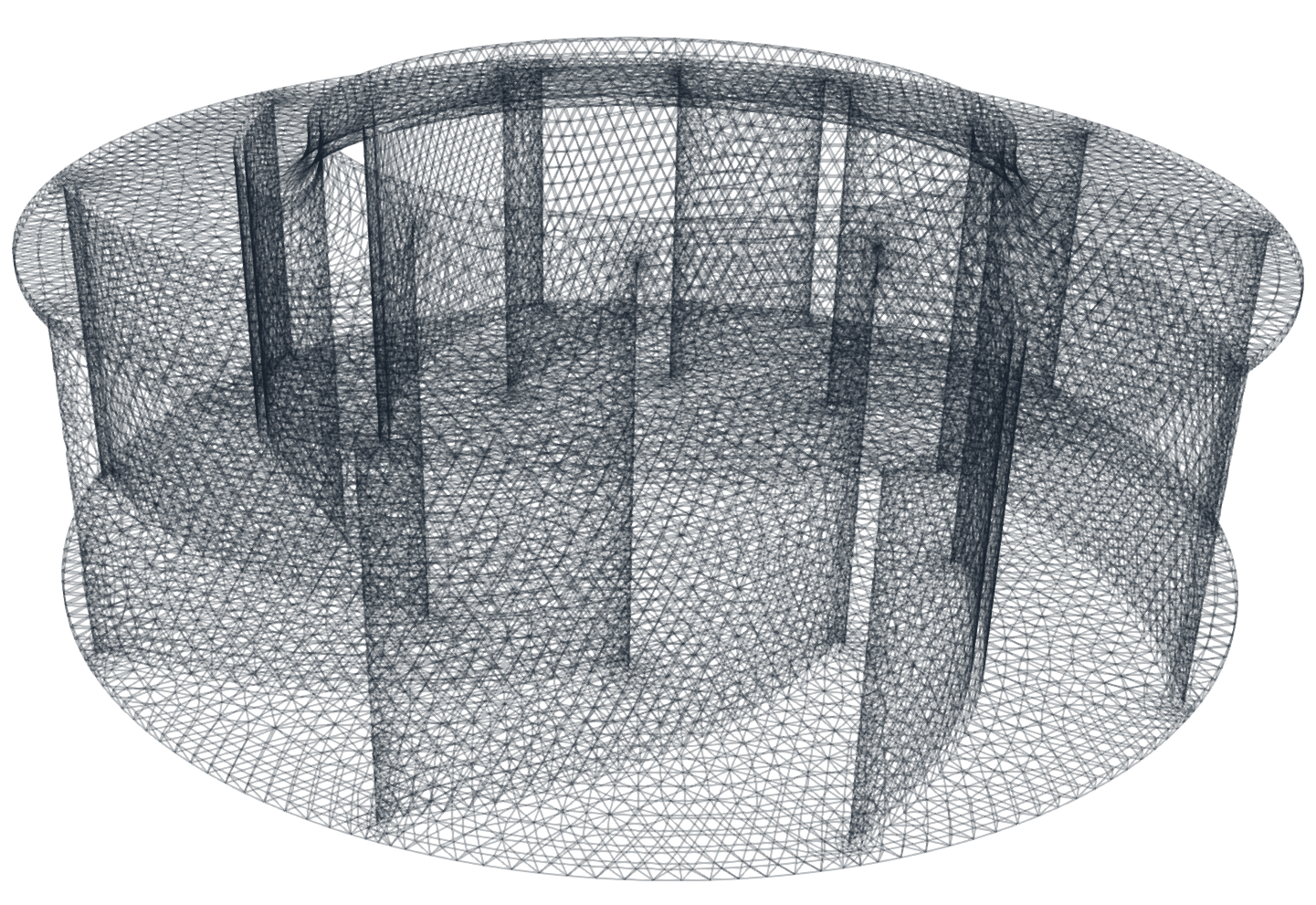
Centrifugal Fan - CFD Simulation Setup
The CFD simulation is managed with TCAE software module TCFD. Complete CFD simulation setup and run is done in the TCFD GUI in ParaView. TCFD uses OpenFOAM open-source application.
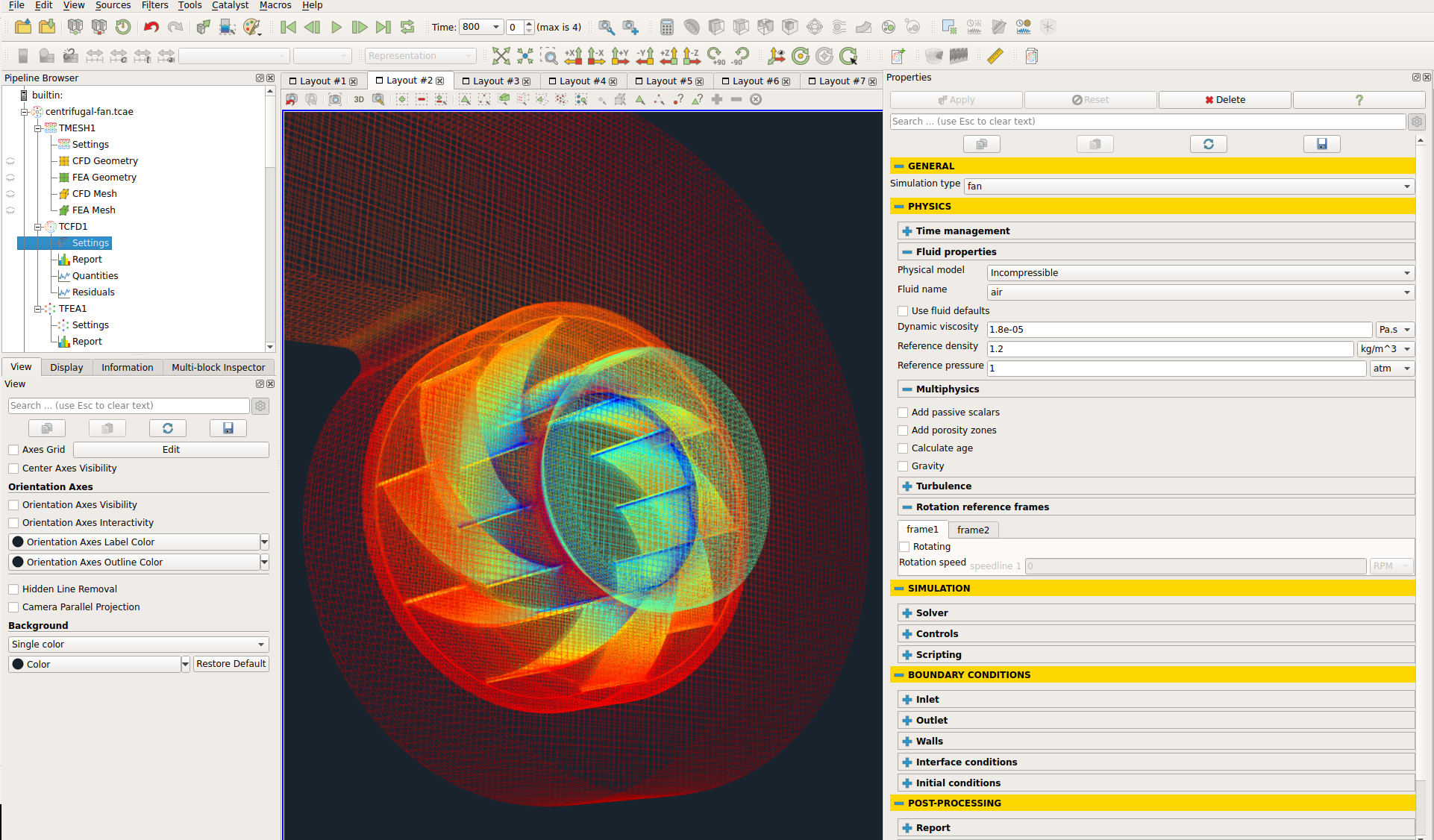
- Simulation type: Fan
- Time management: steady-state
- Physical model: Incompressible
- Number of components: 3 [-]
- Wall roughness: none
- Physical model: Incompressible
- Speed: 3000 [RPM]
- Outlet: Static pressure 0 [m2/s2]
- Turbulence: RANS
- Turbulence model: k-omega SST
- Wall treatment: Wall functions
- Turbulence intensity: 5%
- Speedlines: 1 [-]
- Simulation points: 5 [-]
- Fluid: Air
- Reference pressure: 1 [atm]
- Dynamic viscosity: 1.8 × 10E-5 [Pa⋅s]
- Air density: 1.2 [kg/m3]
- CFD CPU Time: 1.5 core.hours/point
- BladeToBlade: on
Any project simulated in TCFD has its component graph. The component graph shows how the components are organized – the model topology. What is the inlet, the outlet and how the components are connected via interfaces. A simple scheme of the component graph is shown below. The air flow enters the fan in the component suction via interface suction-inlet and leaves the fan from component spiral via interface spiral-outlet. This is a typical example of a very simple linear order of the flow through a combination of three components.
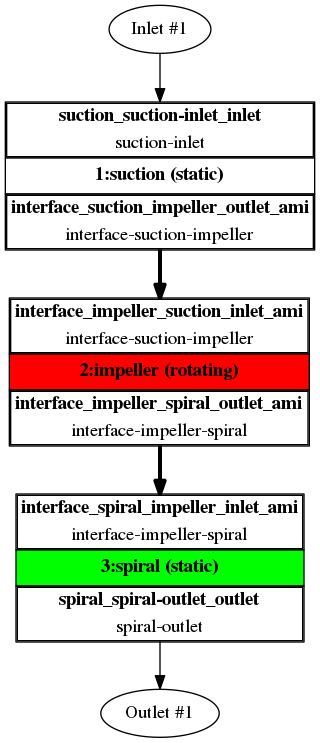
Centrifugal Fan - FEA Simulation Setup
The FEA simulation is managed with TCAE software module TFEA. Complete FEA simulation setup and run is done in the TFEA GUI in ParaView. TFEA uses Calculix open-source application.
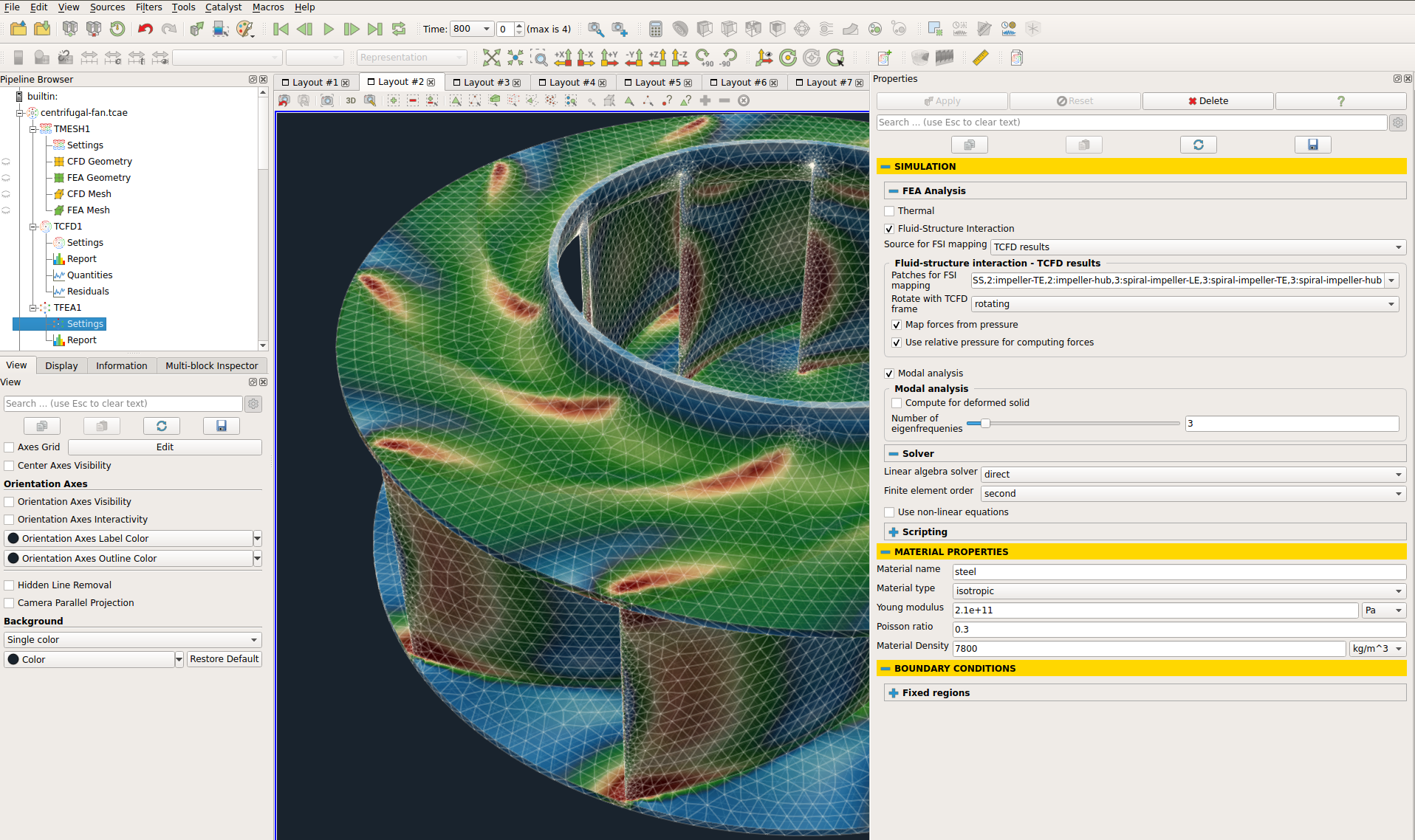
- Beam material: steel
- Material density: 7800 kg/m3
- Material structure: isotropic
- Young modulus: 2.1E11 Pa
- Poisson ratio: 0.3
- Fixed radius: 100 [mm]
- Finite element order: second
- FEA CPU Time: 0.02 core.hours/point
All the simulation data are also saved in tabulated .csv files for further evaluation. TCFD is capable of writing the results down at any time during the simulation. The convergence of basic quantities and integral quantities is monitored still during the simulation run. The geometry was created onetime using TCAD in the preprocessing phase. First, the TMESH is executed to create the volume meshes for CFD & FEA. Then the CFD simulation is executed and evaluated. After that, in the FSI step, the pressure field is integrated to create the force field which is prescribed as a load for the FEA simulation. Finally, the FEA simulation is executed and evaluated.
Centrifugal Fan - TCAE Simulation run
The TCAE simulation run is completely automated. The whole workflow can be run by a single click in the GUI, or the whole process can be run in the batch mode on a background. Modules used are TCAD, TMESH, TCFD, and TFEA. The simulation is executed in the steady-state mode, for five volumetric flow rate values of 32, 28, 24, 20, and 16 m3/s. TCFD includes a built-in post-processing module that automatically evaluates all the required quantities, such as efficiency, torque, forces, force coefficients, flow rates, pressure, velocity, and much more. All these quantities are evaluated throughout the simulation run, and all the important data is summarized in an HTML report, which can be updated anytime during the simulation, for every run.
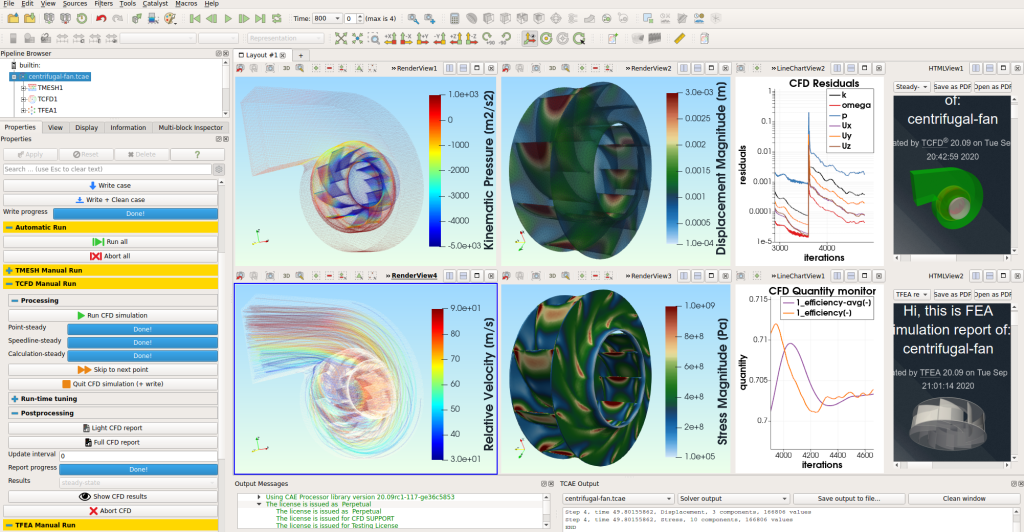
All the simulation data are also saved in tabulated .csv files for further evaluation. TCFD is capable of writing the results down at any time during the simulation. The convergence of basic quantities and integral quantities is monitored still during the simulation run. The geometry was created onetime using TCAD in the preprocessing phase. First, the TMESH is executed to create the volume meshes for CFD & FEA. Then the CFD simulation is executed and evaluated. After that, in the FSI step, the pressure field is integrated to create the force field which is prescribed as a load for the FEA simulation. Finally, the FEA simulation is executed and evaluated.
Centrifugal Fan - Postprocessing - Integral Results
The simulation results are evaluated automatically. Every simulation run in TCAE has its own unique simulation report. The integral results both for CFD and FEA are written down in the following HTML or PDF reports:
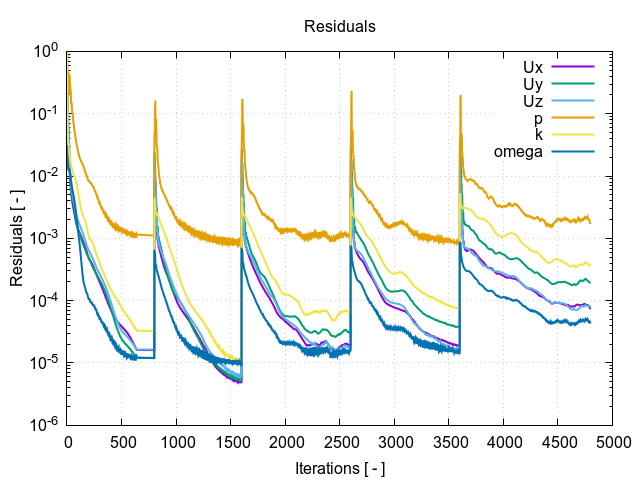
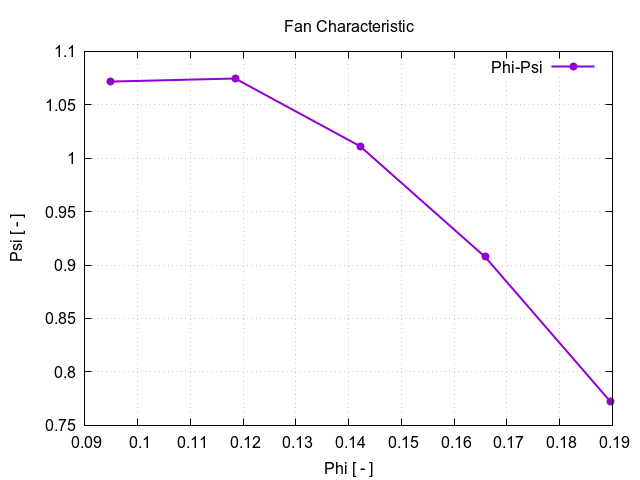
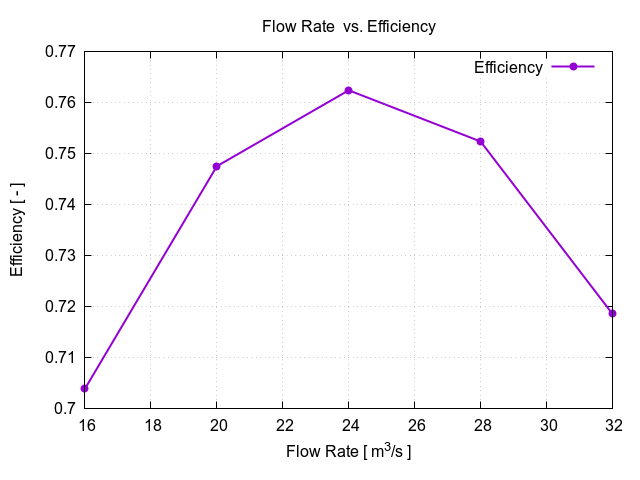
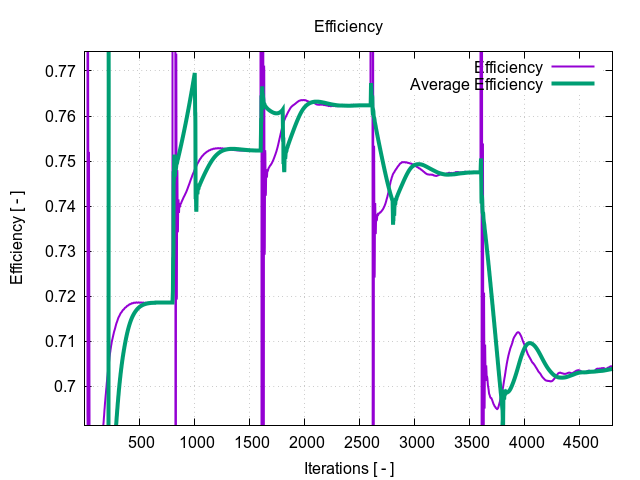
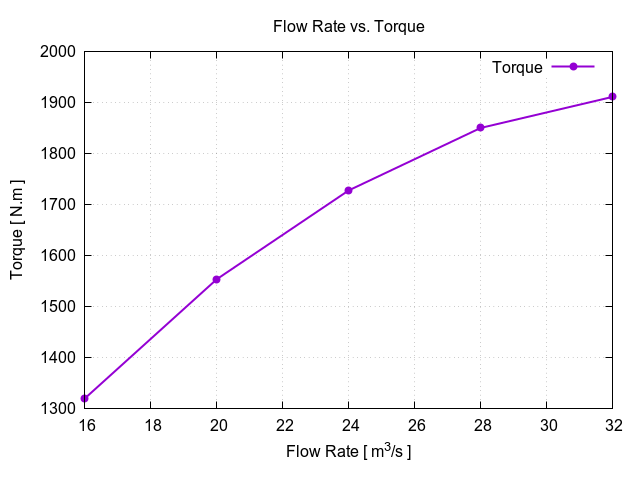
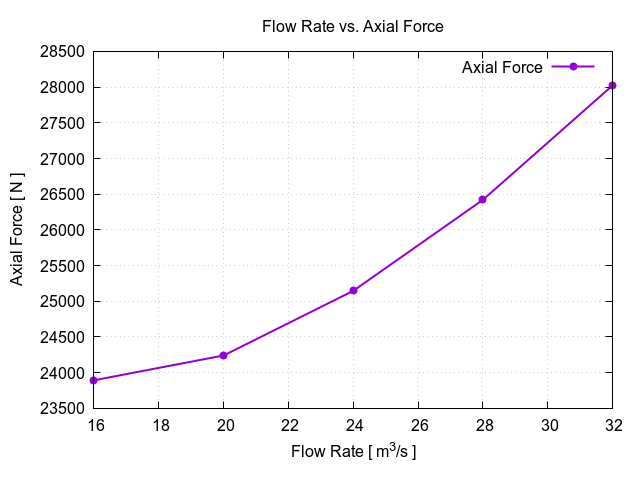
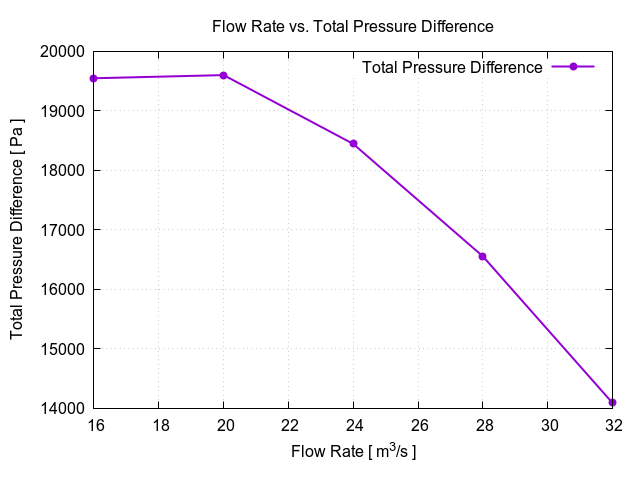
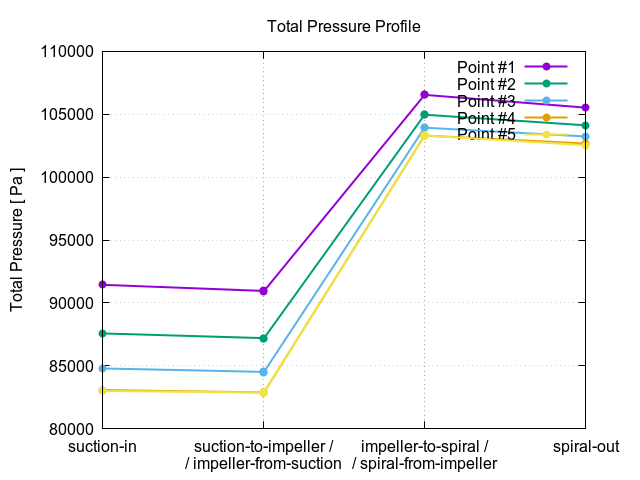
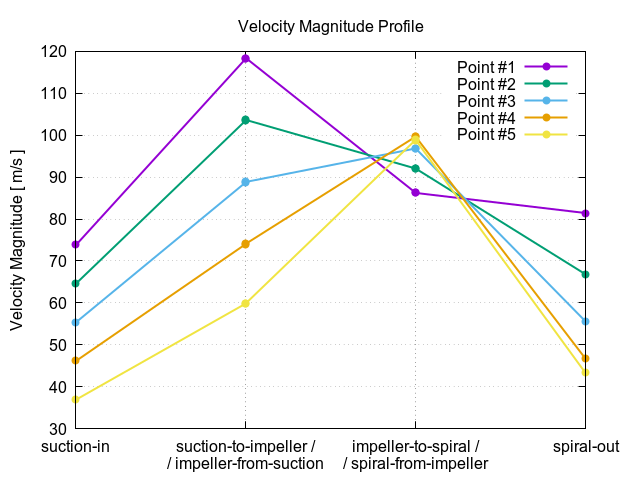
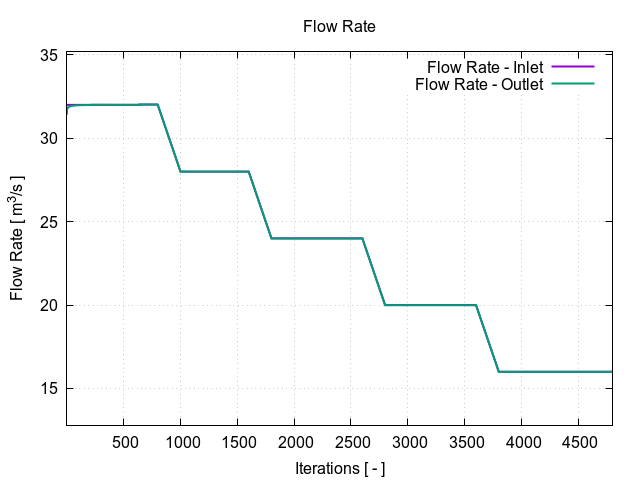
Centrifugal Fan - Postprocessing - Volume Fields
All the integral results are stored in the .CSV files and are available for further postprocessing if needed. The volume fields are postprocessed in open-source visualization tool ParaView. ParaView provides a wide range of tools and methods for CFD & FEA postprocessing and results’ evaluation. There are available countless useful filters and sources, for example: Calculator, Contour, CLip, Slice, Threshold, Glyph (Vectors), Streamtraces (Streamlines), and many others.
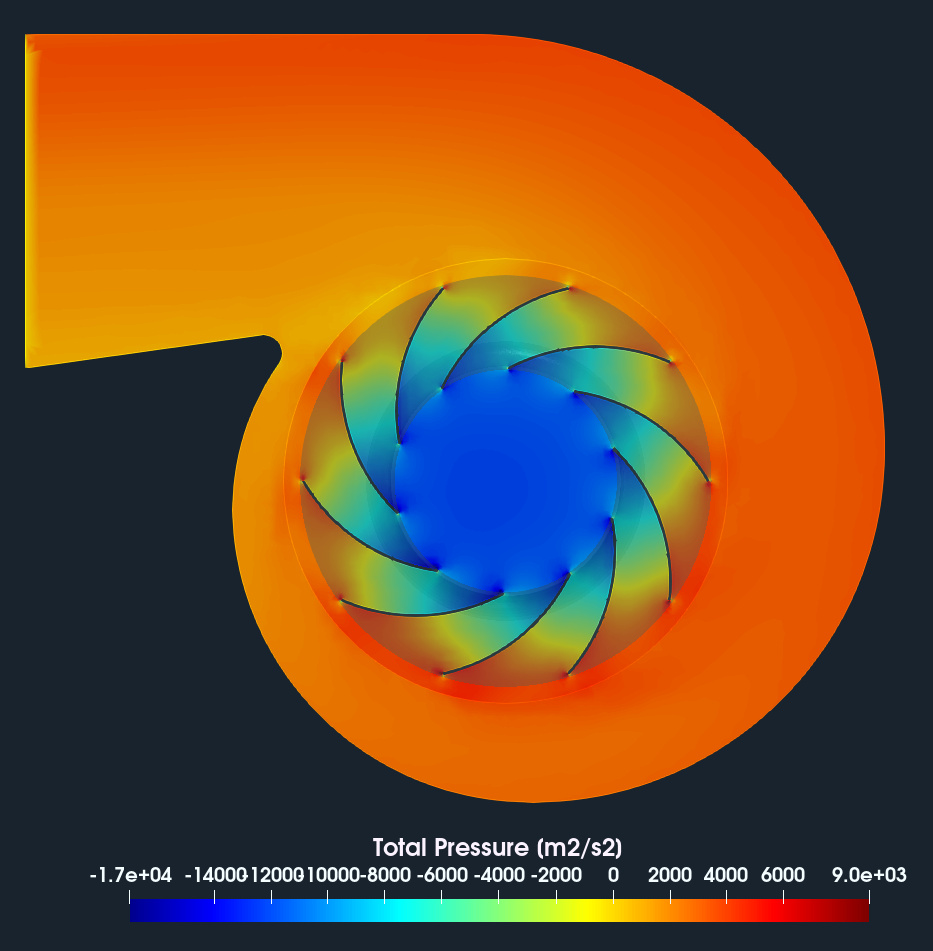
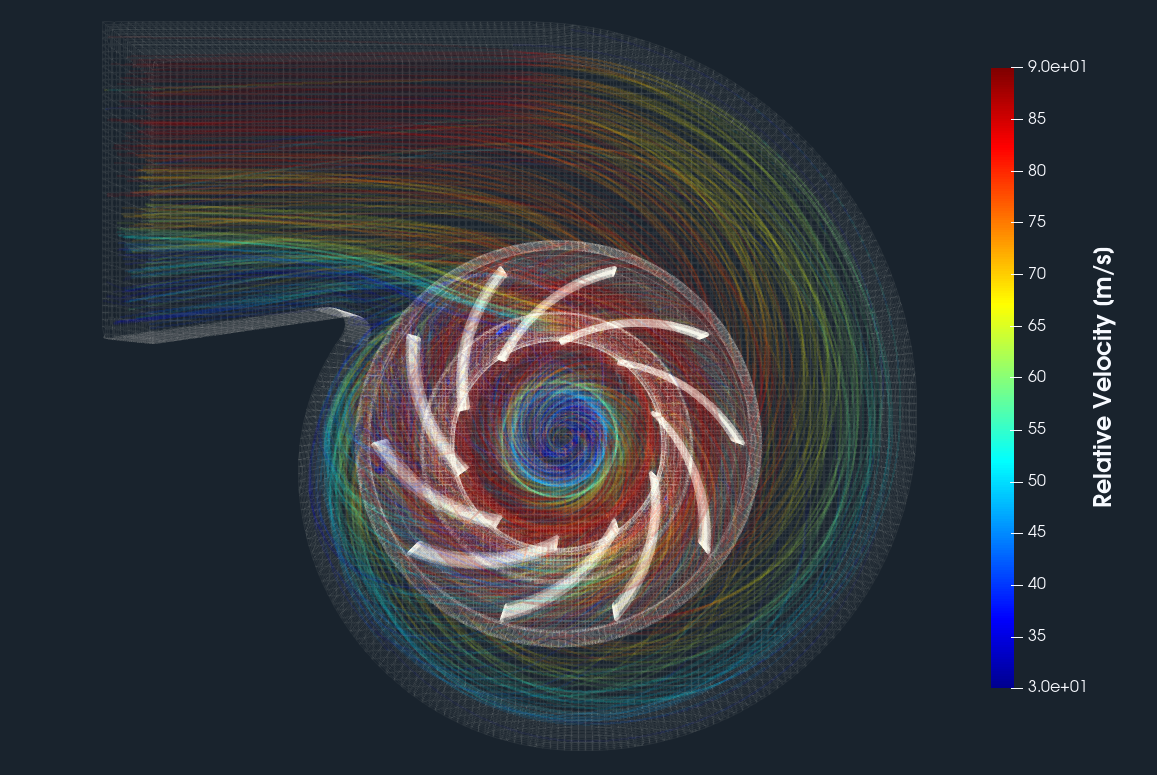
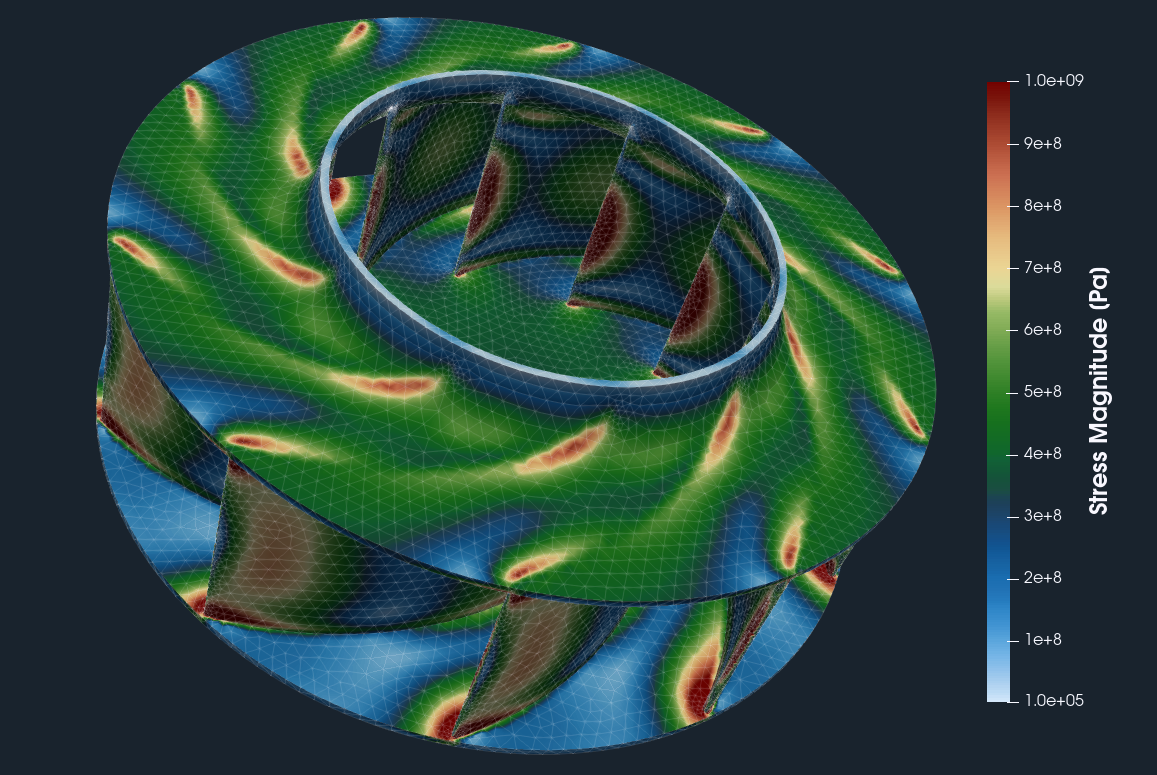
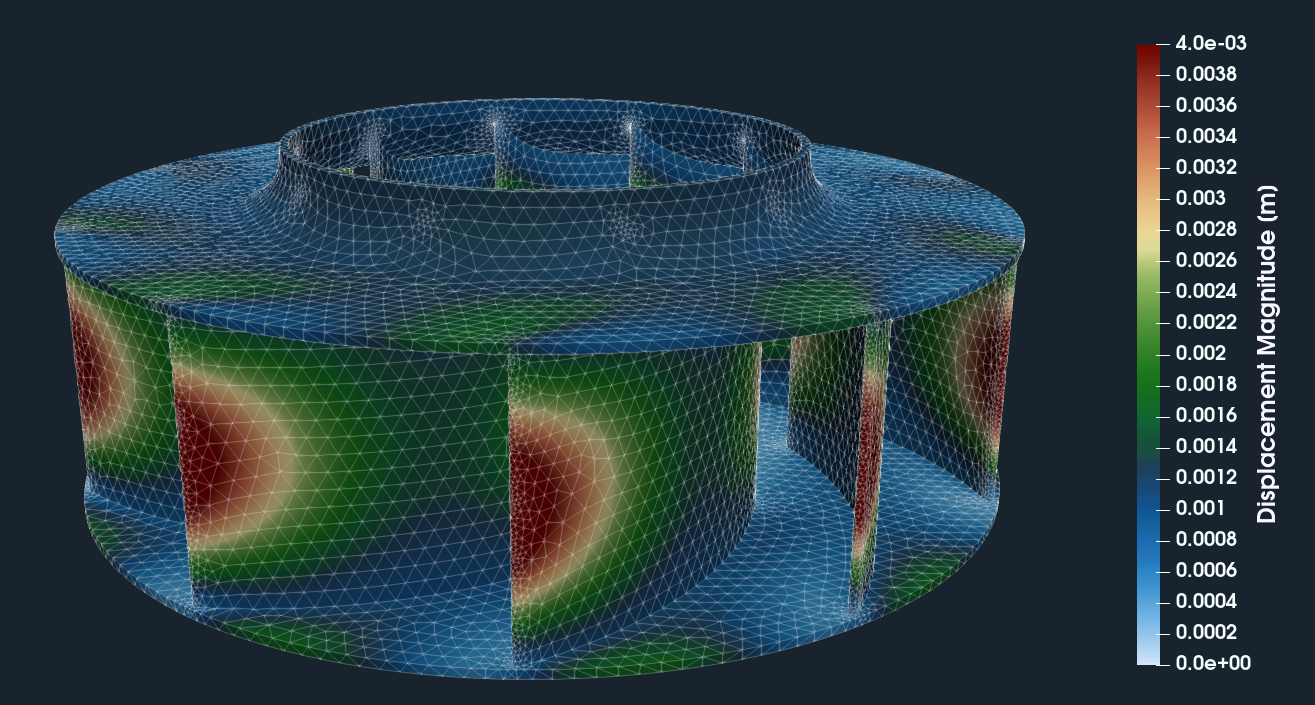
Centrifugal Fan - Turbo Postprocessing
All the integral results are stored in the .CSV files and are available for further postprocessing if needed. The volume fields are postprocessed in open-source visualization tool ParaView. ParaView provides a wide range of tools and methods for CFD & FEA postprocessing and results’ evaluation. There are available countless useful filters and sources, for example: Calculator, Contour, CLip, Slice, Threshold, Glyph (Vectors), Streamtraces (Streamlines), and many others.
Meridional Average
For turbomachinery engineers, it is typically important to see the results, for example, total pressure or velocity, circumferentially averaged and projected on the meridian plane. This method is called the Meridional Average. This meridional average projection avoids the holes (blades) and shows how the total pressure (energy) or velocity are distributed along the meridian (a 2D interpretation of flow through the fan).
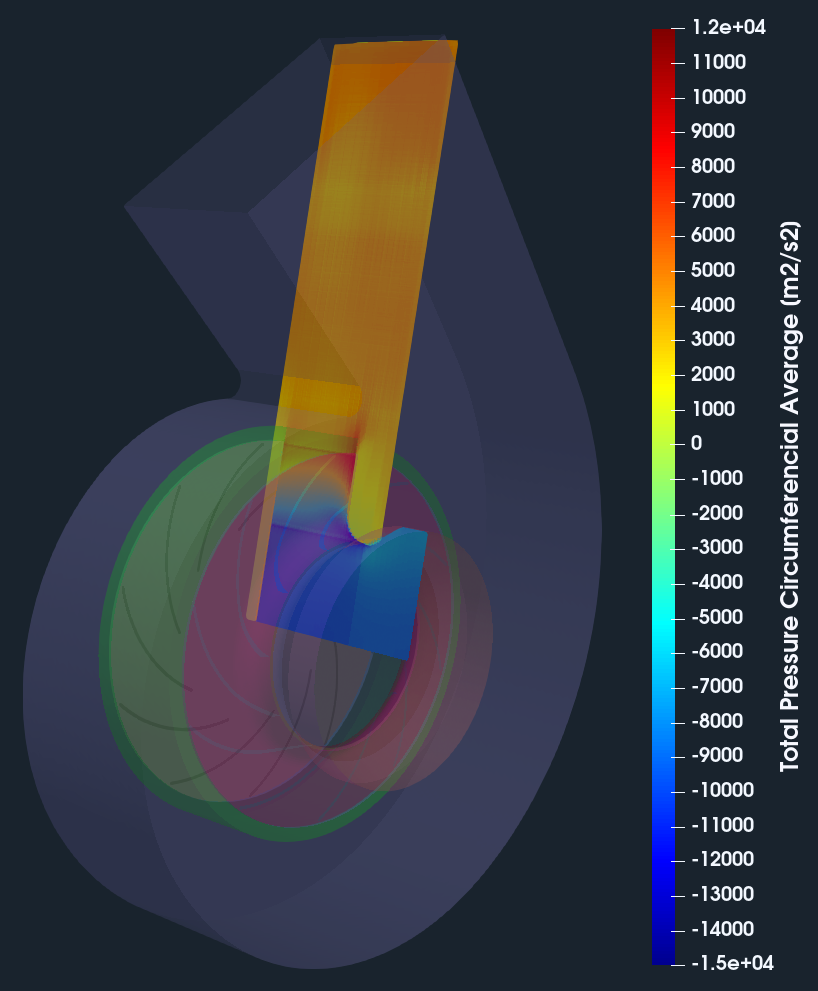
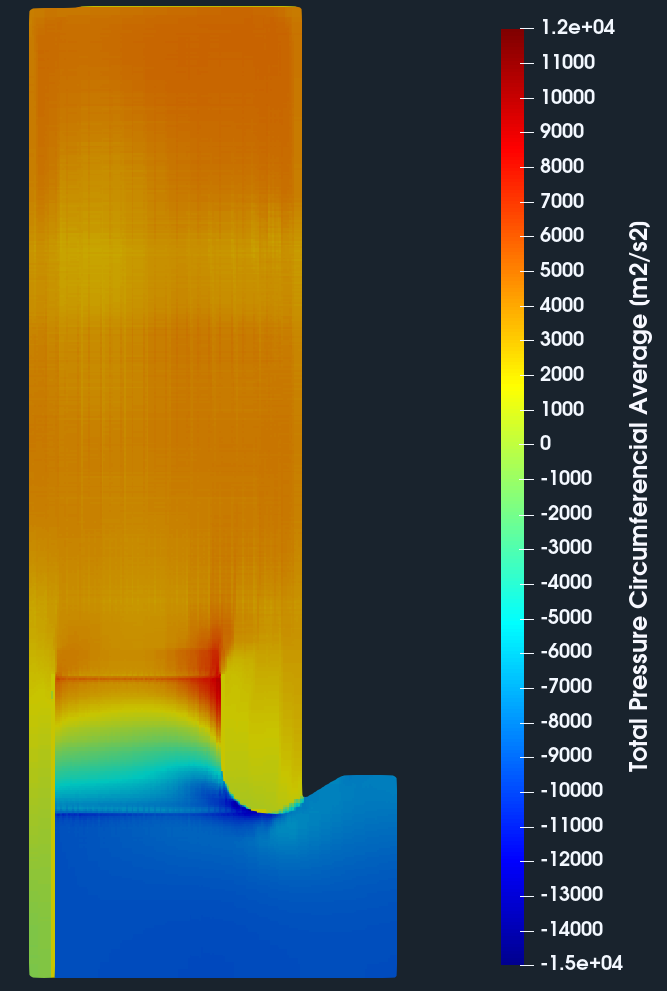
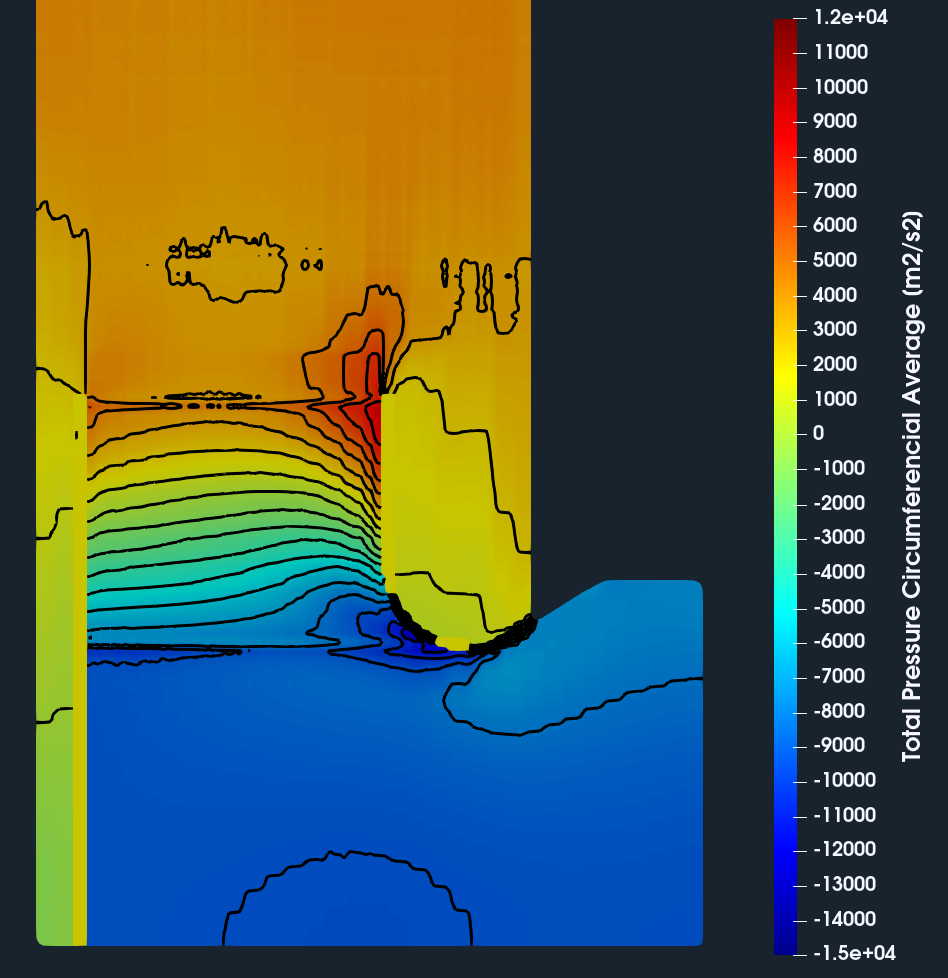
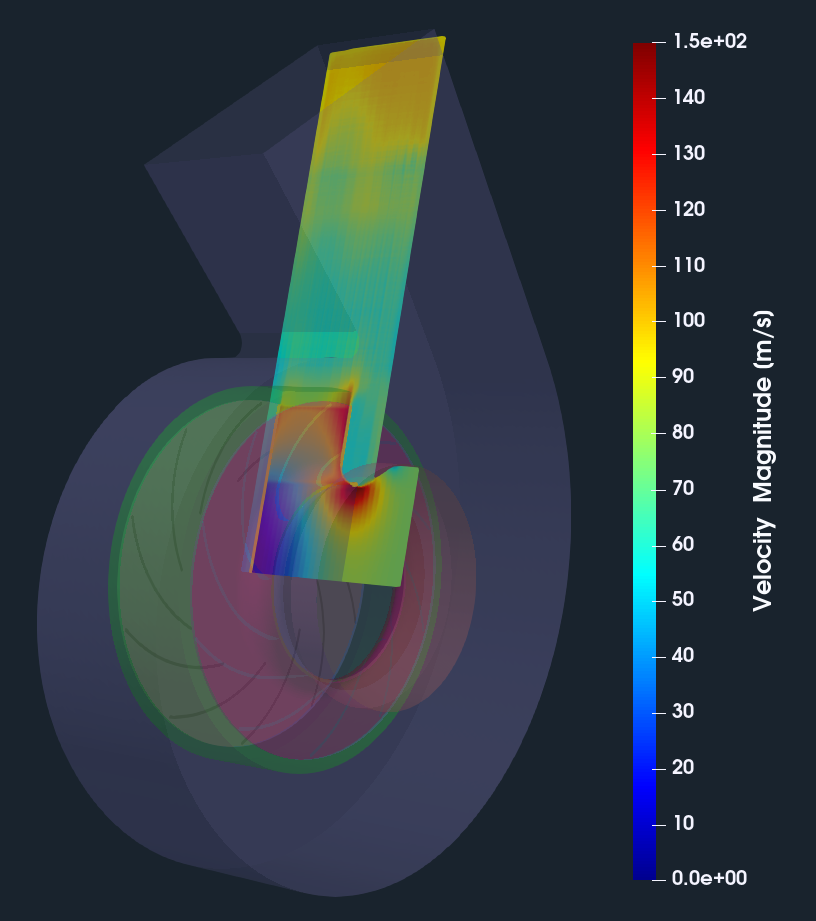
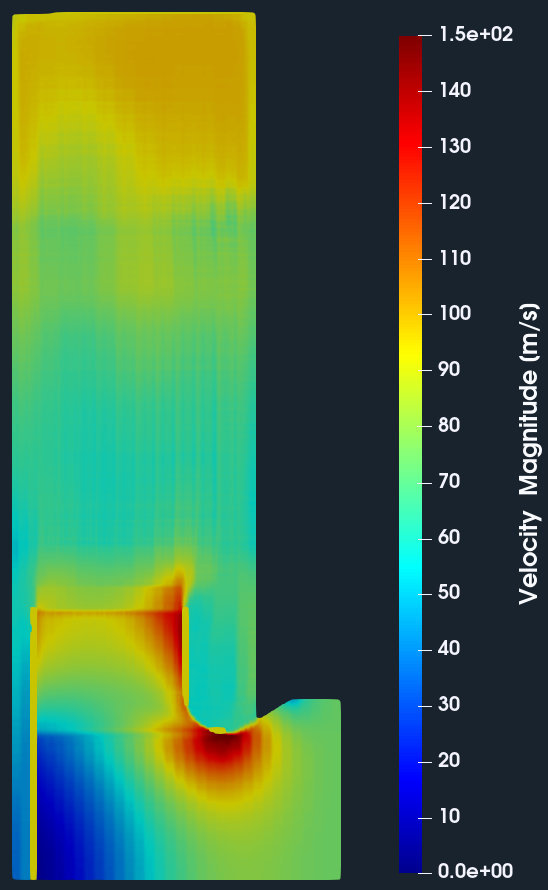
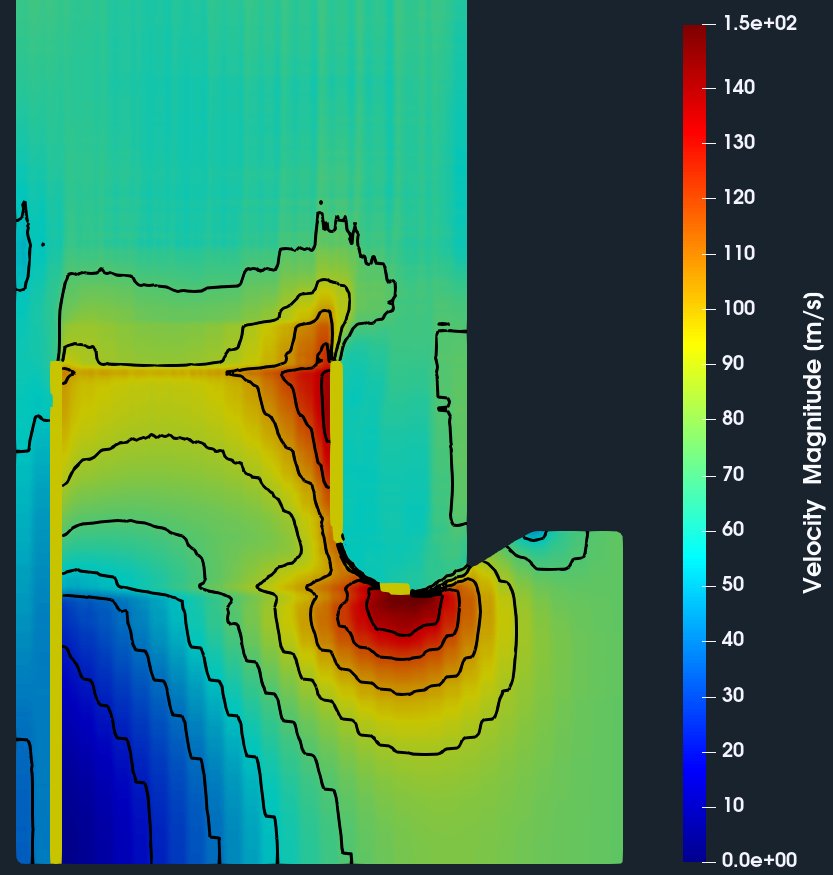
Blade to Blade View
Blade to blade view is a special transformation method that transforms the rotational object (and the CFD results) into the dimensionless hexahedron of edges 2phi x 1 x 1. The blade-to-blade view offers a unique perspective for an inspection of the flow between the blades on a plane at a fixed relative distance between hub and shroud surfaces. Especially, leading and trailing edges (flow angles) are of the main interest here.
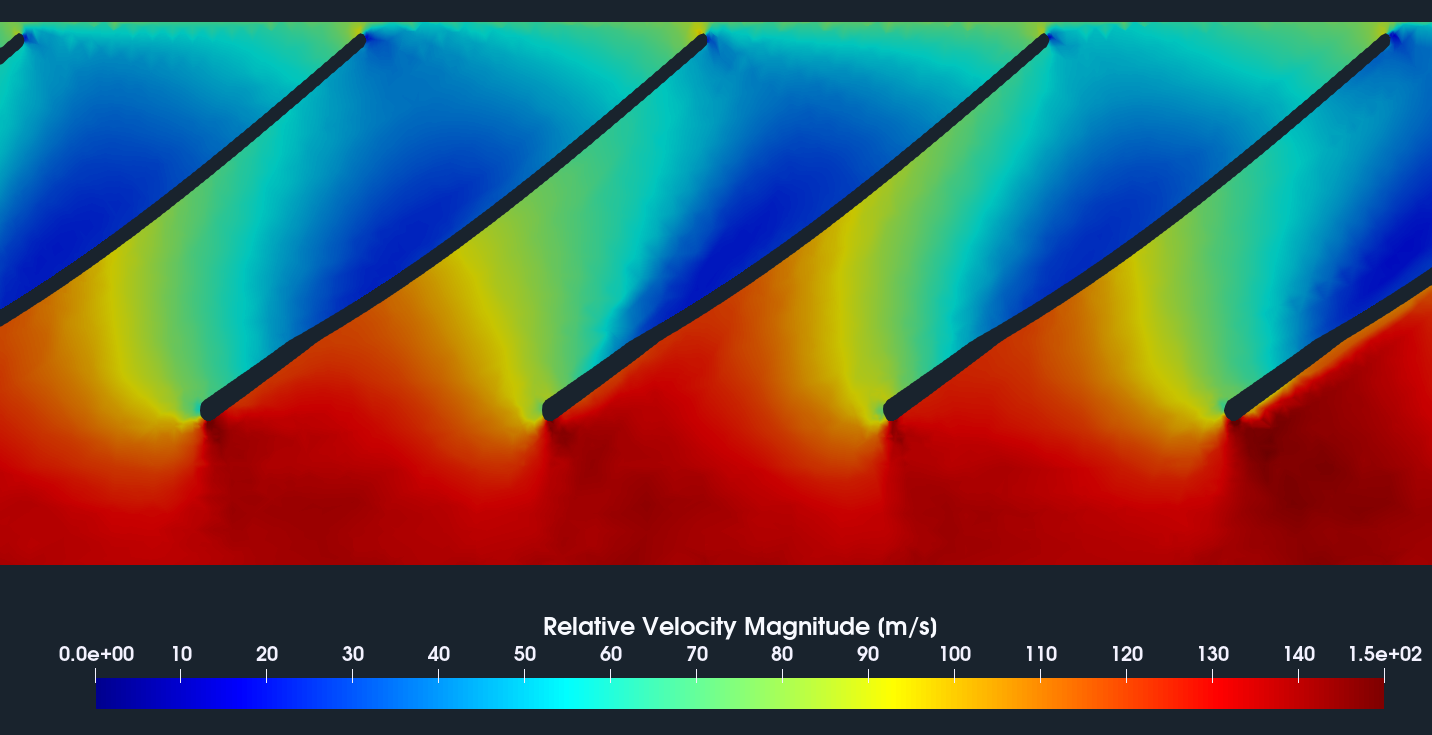
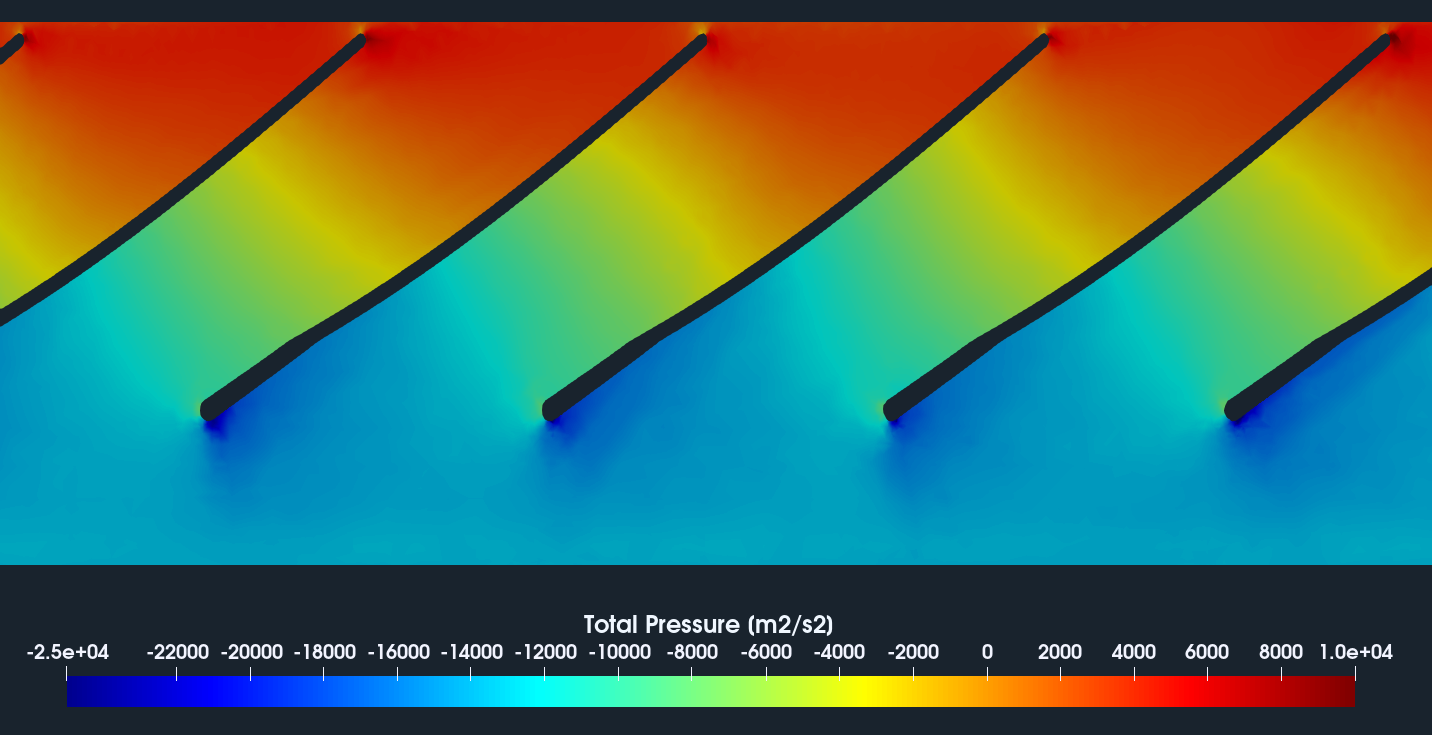
Results Animation
Below, there is an animation of the rotating centrifugal fan (right-hand side) and the deformation (left-hand side) of the impeller due to the inertia and centrifugal forces and forces from the airflow. FYI: The speed of rotation is approximately 135 times slower than the real rotation. The deformation movement is displayed 10 times higher to enhance the details.
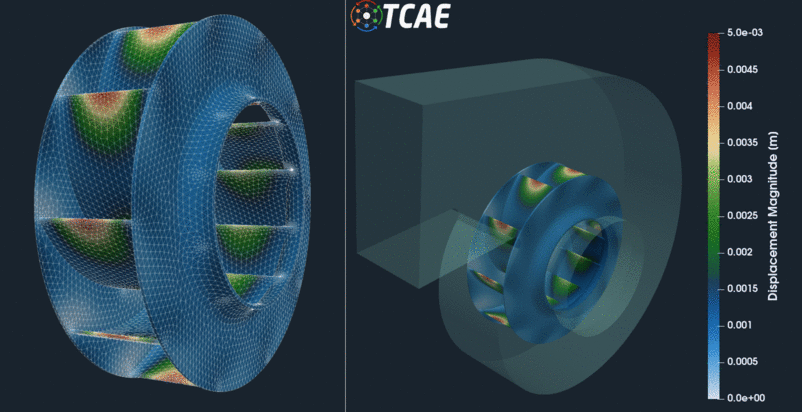
Centrifugal fan - Particle-like Animation
TCAE offers extensive possibilities for flow visualization. Very typical flow visualization is the visualization of stream traces – the trajectories of the flow. Based on stream traces, it is possible to make a visualization of particle-like flow to enhance the flow details. See the following animation. Imaginary particles enter the centrifugal fan approximately at the same time. There are several effects to observe. Some particles stay in the turbine 5-10 times longer than the fastest ones.
Conclusion
• It has been shown how to make a comprehensive CFD & FEA analysis including FSI of the centrifugal fan in a single one automated workflow.
• TCAE showed to be a very well suited tool for CFD, FEA, and FSI engineering simulations.
• More information about TCAE can be found on CFD SUPPORT website: http://www.cfdsupport.com/tcae.html
• Questions will be answered via email info@cfdsupport.com.
References
[1] TCAE Manual
[2] TCAE Training
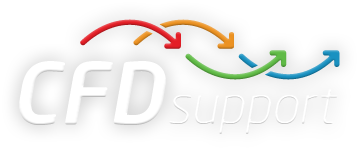